Aktuell intensivierte sich der Modernisierungsprozess der Glasbranche und auch nach der erwarteten Eindämmung der Covid-19-Pandemie, ihrer Verwerfungen des Arbeitsmarkts und der Lieferketten wird die Digitalisierung wohl weiterhin an Dynamik gewinnen.
Ein hoher Automatisierungsgrad mit intern und extern digital vernetzten Systemen erscheint zunehmend als elementare Voraussetzung, um wirtschaftliche Schwankungen besser aufzufangen und dem Fachkräftemangel zu begegnen.
Die europäischen Glas-Maschinenbauer haben ihr Angebot darauf eingestellt und liefern sehr leistungsfähige integrierte Anlagen, die die komplexen, aus vielen Einzelschritten mit höchst unterschiedlichen Tempi bestehenden Fertigungsprozesse – vom Zuschnitt über Kanten-, Ausschnitt- und Flächenbearbeitung, Waschen und Härten – zusammenhängend darstellen können.
Hohe Produktqualität mit niedrigsten Reklamationsquoten, Arbeitssicherheit, Kostenersparnis und Nachhaltigkeit dank Flächen-, Wasser- und Energieeinsparung sind die Vorteile dieser Entwicklung.
Allein die effizientere Beschickung der Härteöfen durch kombinierte technische und logistische Maßnahmen erbringt häufig ein Einsparpotential bei den Energiekosten von mehreren hunderttausend Euro pro Jahr und Werk, ganz zu schweigen von stark verkürzten Auftrags-Laufzeiten.
Für Glas 4.0 muss die Basis stimmen
Offensichtlich ist auch, dass bei der schrittweisen Aneignung von Industrie 4.0-Methoden noch erhebliche Vorarbeiten anstehen. Diese werden nicht immer konzeptionell langfristig geplant, sondern oft erst im Zusammenhang mit dem Ersatz alter Produktionsanlagen, gewissermaßen in einem „Zeitsprung“, vorgenommen.
An dieser Übergangsschwelle im Vorfeld der anstehenden Modernisierung, treten oft kurzfristig eine Reihe neuer Anforderungen zu Tage, über die sich Verarbeiter, Zulieferer und Dienstleister Klarheit verschaffen müssen, insbesondere über
Zur Gewährleistung stabiler Prozesse durch die permanente Verfügbarkeitsprüfung und planbare Instandhaltung der Anlagen spielen Assistenzsysteme eine immer wichtigere Rolle; vor allem:
Die Software- und Hardware-Ausstattung der Flachglasindustrie bildet inzwischen große Schnittmengen mit der IT-Branche, was auch strukturpolitische Probleme stärker hervortreten lässt: der schnellere Verschleiß von Hi-Tech-Anlagen und der durch Automation erleichterte Mehrschichtbetreib senken zwar mit der dann veränderten „betriebsgewöhnlichen“ Nutzungsdauer die AfA-Fristen, jedoch dürften die kürzeren Austauschzyklen der Technik auch Auswirkungen auf das Investitionsverhalten und aus technischer Sicht auf die Serienreife von Anlagen und deren Betriebssoftware bedeuten.
Wie definiert sich zukünftig eine „ausgereifte“ Produktionsmaschine? Beruhen Solidität und Störungssicherheit zukünftig vor allem auf digitalen Torsionsanalysen, Sensorik und Überwachungssoftware statt auf Erfahrung und empirisch-technischer Evolution?
Welche Rolle spielt zukünftig der technische Service als ehemals wichtigste Schnittstelle zwischen Anwendern und Produktentwicklern?
Technische „Generationsprobleme“ bescheren Betreibern und Service-Dienstleistern gerade am Beginn der Anlagenvernetzung erhöhten Aufwand: immer wieder müssen Taktzeiten, Signalpegel, Software und Steuerungshardware unterschiedlicher Maschinenzeitalter angeglichen werden, um die sichere, zertifizierbare Funktion in verbundenen Anlagen herzustellen.
Dies darf nie kompromissbehaftet sein und ist so für die beteiligten Partner eine große Herausforderung. Die Umstellung von Technik und Logistik auf 4.0 taugliche Standards ist so kein statischer Vorgang, sondern erfordert Kreativität bei der Überwindung zahlreicher praktischer Hemmnisse in Gestalt technischer Inkompatibilitäten.
Der Zugriff auf die erforderliche über lange Zeiträume geführte technische Dokumentation und auf aktuelles Know-how setzt für Serviceunternehmen eine langfristige, fast symbiotische Kooperation mit den Herstellern der Maschinen voraus. Unter diesem Aspekt kann die Glastechnik Holger Kramp in von längjährigen verlässlichen Kooperation mit den überwiegend italienischen Maschinen-Partnern gut profitieren.
Ein zweiter Aspekt ist die wachsende Produktvielfalt durch kleine, individualisierte Losgrößen. Der von den Glasgroßhändlern und Onlineshops immer ungeduldiger ausgeübte Marktdruck fordert von Glasverarbeitern ene höherer Flexibilität. Deren Maschinenpark muss zwangsläufig mit minimalen Rüstzeiten auskommen und Produktumstellungen innerhalb weniger Minuten, ja Sekunden, vornehmen können. Damit geht eine zeitliche Intensivierung von Einstellvorgängen, mechanischen und elektrischen Lastwechseln einher, die nicht ohne Folgen bleibt.
Hinzu kommt eine erhöhte Bandbreite der Produktformate und die enorme Verdichtung von Funktionen innerhalb der Produktionsanlagen, die durchgängiges Glas-Handling, Zuschnitt, Parametrisierung, mehrstufige CNC-Bearbeitung, Waschen, Glas-Transport und Lagerung mit „intelligenter“ Logistik beherrschen.
Viele der modernen Systeme verbindet, dass damit neben der automatischen auch manuelle Bearbeitungen für Sonderanfertigungen, beispielsweise für die Produktentwicklung, möglich sind.
Diese vollintegrierten Systeme werfen so neue und schärfere Fragen zu Anlagensicherheit, Ausfallbeständigkeit und Redundanz auf.
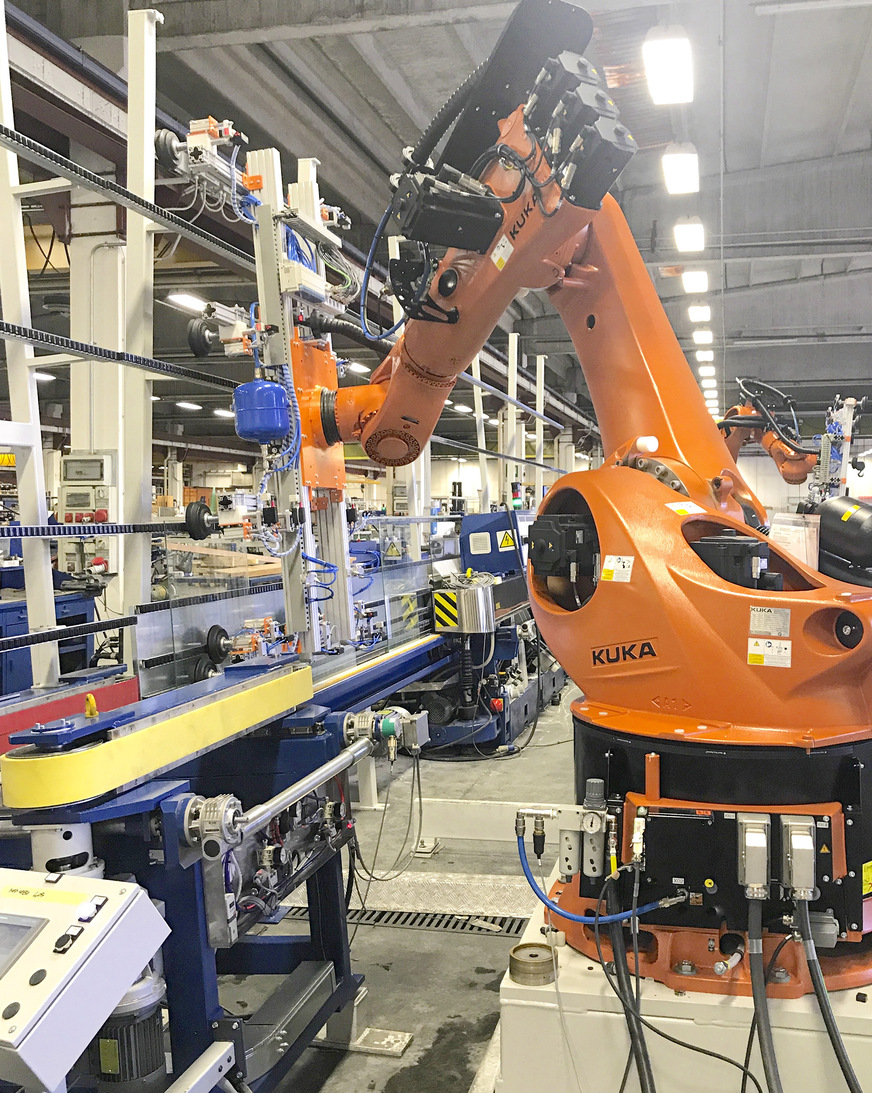
Foto: Elettromeccanica Bovone Srl
Vorbeugender Service gewinnt deutlich an Bedeutung
Wir empfehlen Betreibern komplexer Anlagen, die bislang meist ad hoc erfolgenden Abrufe von Servicetechnikern durch planmäßige Anlageninspektionen und Wartungen auf vertraglicher Grundlage zu ersetzen. Diese sollten jedoch keine Formalie unter allgemeinen Pflichtterminen sein, sondern auf messbaren technischen Kriterien beruhen.
Bereits heute lassen sich die in der Betriebssoftware vieler Maschinen erfassten Maschinenlaufzeiten mit Verschleißangaben der Hersteller von Maschinenkomponenten abgleichen und per Software auswerten.
Anhand von individuellen Produktionsdaten, die nach einer Neu-Installation innerhalb der Gewährleistungsfristen erfasst werden können, lässt sich so die Wartungsplanung der Produktionsleitung und der Instandhalter konkret aufbauen. Damit ist ein wirksames Mittel gegen ungeplante Stillstände durch das Warten auf Lieferungen spezifischer Ersatzteile gegeben.
Einen vollständig „automatisierten“ Umgang mit den sehr vielfältigen Serviceproblemen wird es, nach unserer Auffassung, auch auf lange Sicht nicht geben. Viele Serviceprobleme unserer Kunden sind nach wie vor auf nicht planbare, plötzlich auftretende Ereignisse zurückzuführen. Spontane Ausfälle durch Verschleiß oder vorzeitige Ermüdung von Maschinenkomponenten, Bedien- oder Wartungsfehler, Wasser- oder Überspannungsschäden kommen mindestens ebenso zufällig auf die Servicetechniker zu wie das Einrichten oder Umsetzen von Maschinen, die am Gebrauchtmarkt erworben wurden.
Die möglichen Konsequenzen von Folgeproblemen kleinerer Defekte in komplexen Systemen machen neben der Schaffung hinreichender Redundanz ein qualifiziertes Monitoring unbedingt erforderlich. Angesichts der zunehmenden Eliminierung menschlicher Eingriffe in die Maschinenfunktion und in den unmittelbaren Fertigungsprozess treten naturgemäß analytische und kommunikative Fähigkeiten der Anlagenbediener und Servicedienstleister in den Vordergrund.
Eine wichtiger Konstante im Alltagsgeschäft ist daher für uns die Kultivierung einer Service- und „Kümmerer“-Mentalität; in erster Linie der Bereitschaft zum Dialog, zum nachhaltigen Support der Anlagenbediener und zur schnellen Reaktion bei auftretenden Problemen.
Dazu gehört ebenso ein entwickeltes Gespür für erforderliche prophylaktische Beratung, um die hochwertigen Investitionen der Kunden in „ruhigem Fahrwasser“ zu betreiben. Aktuell lässt diese zwar der Zeitaufwand der Personal- und Ressourcenplanung der Serviceeinheiten ansteigen, unter anderem infolge der Teil-Verlagerung von BackOffice-Tätigkeiten in Homeoffices. Jedoch Online-Meetings zu akuten Problemfällen oder zu komplexen Ressourcenplanungen sind dabei nur schwer zu vergleichen mit persönlichen Beratungen, in denen sich die Mitarbeiter differenzierter einbringen können.
Auch die in Folge der Pandemie erforderlichen zusätzlichen Investitionen in die digitale Infrastruktur halten noch nicht Schritt mit den organisatorischen Anforderungen. Die hierfür benötigten Mittel sind noch zusätzlich aufzubringen; die Ressourcen werden zudem von anderen Prioritäten stark beansprucht, so zur Kompensation von Ausfällen nach Zulieferer-Lockdowns, zur erweiterten Bevorratung mit Ersatzteilen, Werkzeugen und Verbrauchsmaterial.
Mit Überwindung dieser Defizite lässt sich jedoch ein weiterer Schritt in Richtung einer effizienteren, ressourcenschonenden und nachhaltigen Arbeitsweise gehen.
Dass dies gegenwärtig erhebliche zusätzliche Anstrengungen und einen kühlen Kopf erfordert, dürfte allen Beteiligten klar sein.
Willi Kühnel, Vertriebsleiter bei Holger Kramp
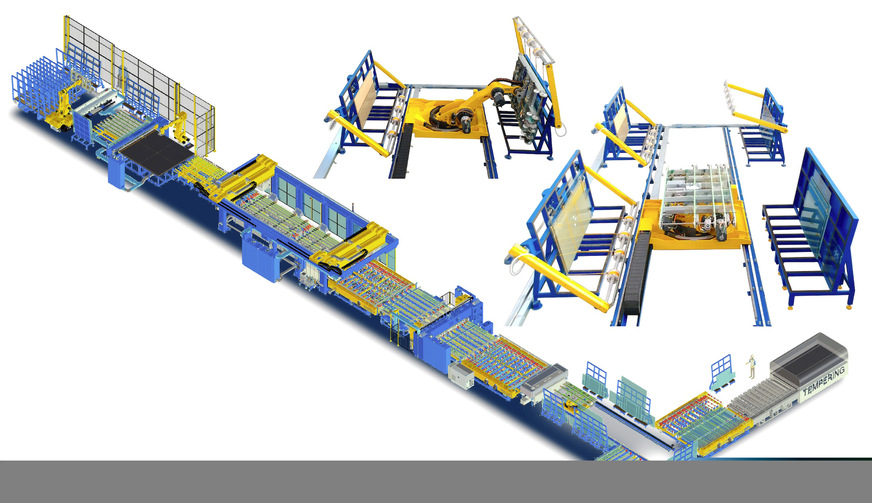
Foto: Forvet