Um die Produktionsprozesse in der Holzfensterbeschichtung noch effizienter zu gestalten und gleichzeitig die Kapazitäten auszuweiten, entschied sich Jan Sehlmann vor einiger Zeit zur Investition in eine komplett neue Anlagentechnik. „Wir sind in unserer zweistöckigen Fertigungshalle räumlich sehr begrenzt. Wir hatten zuvor nur einen Fertigungskreislauf, was uns zeitlich sehr eingeengt hat. Es war nicht einfach und oft mit Stress verbunden, im Takt zu bleiben. Daher haben wir nach einer Möglichkeit gesucht, unsere Arbeitsprozesse zu optimieren und flexibler zu gestalten“, so der Geschäftsführer und leidenschaftlicher Holzfensterproduzent.
Fenster fahren mit dem Aufzug
Vor diesem Hintergrund holte man sich die Experten von Range + Heine dazu. Und diese planten für Sehlmann Fensterbau eine genau auf die Anforderungen und die beengten Platzverhältnisse ausgerichtete Anlagentechnik – und zwar über zwei Etagen. R+H Geschäftsführerin Claudia Max-Heine erklärt: „Um die örtlichen Gegebenheiten optimal auszunutzen und den Beschichtungsprozess zu optimieren, haben wir einen speziellen Aufzug zur Förderung der Werkstücke vom Erdgeschoss in die erste Etage geplant und realisiert. Das war eine ganz besondere Ingenieursleistung und auch für unser erfahrenes Team keine alltägliche Herausforderung.“
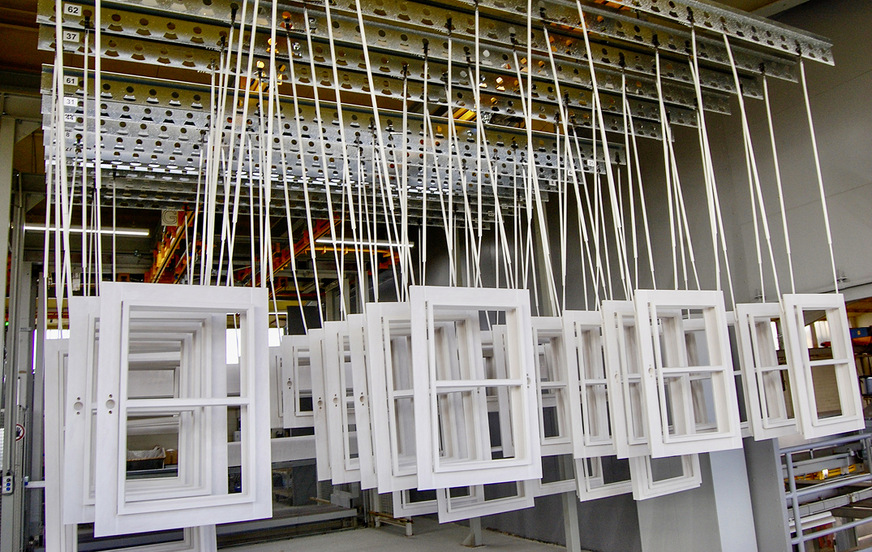
Foto: Range + Heine
Leitrechner zur Prozessoptimierung
Herzstück der neuen Anlage ist der eigens von Range + Heine gebaute Leitrechner – dieser steuert und begleitet den gesamten Fertigungs- bzw. Beschichtungsprozess. Vor Beginn kann der Bediener am Touchdisplay die einzelnen Prozessschritte und -zeiten sowie die Farbgebung der zu lackierenden Bauteile komplett vorkonfigurieren. Die Daten werden dann über einen Chip an der Traverse im System mitverfolgt, so dass der Farbwechsel an der Flutanlage und am Roboter sowie die richtige Weichenstellung in der Fördertechnik komplett automatisch und ohne manuelle Eingriffe erfolgen. Dabei haben die Mitarbeiter den Produktions- und Beschichtungsprozess von einem zentralen Arbeitsplatz im Erdgeschoss immer im Blick und können auch die Abläufe im Oberschoss jederzeit einsehen. Claudia Max-Heine: „Der Leitrechner ist ein wesentlicher Baustein zur Industrie 4.0 und so konfiguriert, dass der Bediener nicht mehr programmieren muss, sondern über einfache Parametrisierung arbeiten kann und leicht zurechtkommt.“ Und: In den nächsten Monaten ist zudem die vollständige Anbindung der Produktionssoftware 3E am Leitrechner geplant.
Effizienter Flut- und Trocknungsprozess
Der Beschichtungsprozess vollzieht sich mit der neuen Anlagentechnik wie folgt: Zunächst werden die Holzelemente manuell an Traversen gehängt – zur Steigerung der Arbeitsergonomie mit Hilfe einer Personen-Hebebühne. Über die Fördertechnik gelangen die Bauteile zu den einzelnen Stationen. In den ersten Schritten erfolgen die Imprägnierung, Grundierung und die Zwischenbeschichtung der Elemente in der Flutanlage. Dabei überzeugt die dort eingesetzte Anlagentechnik durch einen besonders hohen Materialausnutzungsgrad von 98 Prozent oder höher. Auch bei Farbwechseln und der Reinigung wird der Lackverlust minimiert. Nach Durchfahren der Flutanlage erreichen die Holzrahmen bzw. Flügel einen speziell eingehausten Abtropfbereich mit Wanne. Diese nimmt den abtropfenden Lack auf und führt ihn wieder in die Flutanlage zurück. Durch eine zusätzliche Luftbefeuchtung und die Optimierung des Abtropfverhaltens – die definierte Abtropfzeit beträgt ca. 15 Minuten – werden der Lackverlust und der spätere Aufwand der Nachbearbeitung minimiert. Im nächsten Schritt erfolgt die Flutlacktrocknung. Der Einsatz eines modernen Halogensystems ermöglicht in 50 Minuten eine schonende Trocknung der Holzteile über Lichtstrahlen. Dabei sorgt die Technologie für einen besonders effizienten Trocknungsprozess von innen nach außen – was unter anderem die Blockfestigkeit der Holzelemente erhöht. Nach der Trocknung erfolgt das manuelle Schleifen der Werkstücke in hängendem Zustand – so entfällt das aufwendige Auf- und Abhängen.
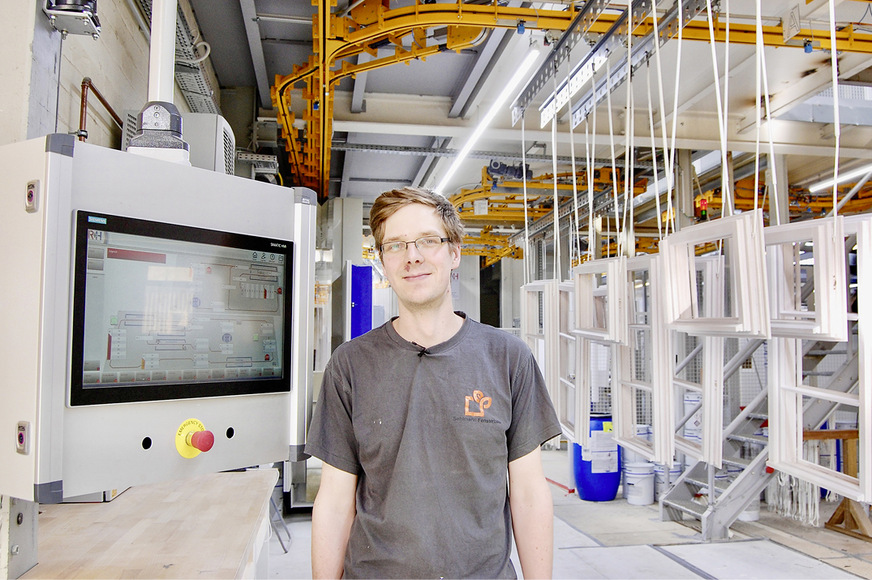
Foto: Range + Heine
Vollautomatische Beschichtung per Robotertechnik
Darauffolgend werden die Traversen mit den Werkstücken per Aufzug in die obere Etage der Fertigungshalle gefördert. Dort erfolgt dann die Spritzlackierung per CMA-Lackierroboter. Dieser ist in einer Lackierkabine platziert und verfügt über neueste 3D-Erkennung: Das Element wird beim Einfahren gescannt und über eine Dicken- und Schräglagenerkennung genauestens eingemessen. Daraufhin wird das jeweilige Lackierprogramm automatisch ausgelöst. Die Kabine wurde mit zwei Absaugwänden konzipiert. Zwischen diesen fährt die Traverse hin- und her – dies sichert sehr geringe Lackierzeiten.
Wladimir Leinweber, Fertigungsleiter bei Sehlmann, erläutert: „Durch die 3D-Erkennung haben wir das Lackieren auf ein neues Niveau gebracht. Der Roboter fährt immer parallel zur Werkstückoberfläche und Schichtstärkenunterschiede in Folge schräger Aufhängungen werden vermieden.“
Nach der Spritzlackierung und der Trocknung werden die beschichteten Bauteile wieder zurück ins Erdgeschoss an den Abhängeplatz transportiert. Insgesamt verfügt die neue Anlage über 60 Traversen. Damit lassen sich unterschiedlichste Fenster-Arten und Geometrien in Abmessungen von bis zu 4 m Länge und 2,70 m Höhe verarbeiten – vollautomatisch gesteuert, in höchster Qualität und nahezu ohne manuelle Nacharbeiten.
Overspray weiter reduziert
Nicht zuletzt spielte bei der Anlagenplanung auch die Schonung der Umwelt und der Ressourcen eine wichtige Rolle. Die Flutanlage arbeitet beispielsweise mit einer sehr hohen Materialeffizienz und hilft so dabei, eine bedeutende Menge Lack einzusparen bzw. dem Produktionskreislauf wieder zuzuführen. Der Lackierroboter ist mit einer AirMatic Zerstäubungsoptimierung ausgestattet. Das bedeutet: Der Sprühstrahl ist deutlich effizienter und noch genauer auf das Werkstück ausgerichtet. So lässt sich im Ergebnis der Overspray und somit der Lackeinsatz um rund 10 bis 15 Prozent reduzieren – bei gleicher Beschichtungsqualität. Zudem sind die Spülzeiten des Lackierroboters sehr kurz; der Spülprozess gestaltet sich vollautomatisch und mit sehr geringem Wasserbedarf (Lackverlust bei Farbwechseln: 1 Liter).
Ein weiteres intelligentes Detail: Die Ecola Vorabscheider – klappbare Wände an beiden Seiten der Spritzkabine. Wenn sich dort in Folge des Lackierprozesses eine Lackschicht aufgebaut hat, lässt sich diese ganz einfach wie eine Tapete abziehen und entsorgen. Rund 60 Prozent des Oversprays bleiben auf den Wänden – diese bestehen aus drei Ebenen versetzter Lochplatten – haften, bevor es in die Verbrauchsfilter geht. Dies sorgt wiederum dafür, dass die Verbrauchsfilter nur selten ausgetauscht werden müssen und im Hausmüll entsorgt werden können. Nicht zuletzt bleibt die Absaugleistung dauerhaft kontant – was eine saubere Kabinenluft garantiert.
Fenster werden haltbarer
Mit dem Ergebnis zeigen sich Jan Sehlmann und seine Mitarbeiter in der Fertigung hochzufrieden: „Die Anlage trägt perfekt dazu bei, unsere Prozesse zu optimieren und unsere Kapazitäten noch besser auszunutzen. Und natürlich können wir damit auch unseren hohen Qualitätsanspruch unterstreichen. Unsere Fenster brauchen 15-20 Jahre keinen neuen Anstrich im deckenden Bereich. Ein tolles Projekt, dass unser Team gemeinsam mit R+H erfolgreich umsetzen konnten. Vielen Dank dafür.“
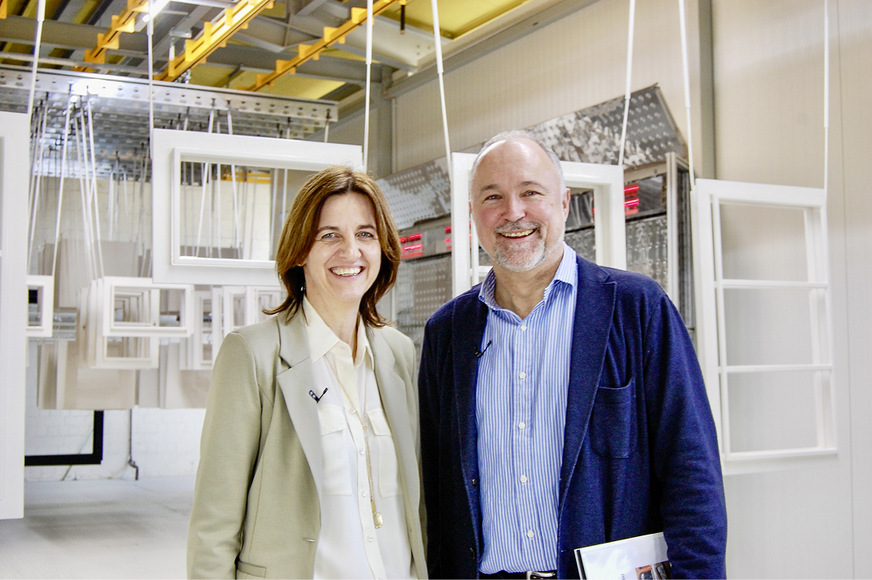
Foto: Range + Heine
Fensterbauer mit hohen Qualitätsansprüchen
Seit mehr als 85 Jahren ist die Sehlmann Fensterbau GmbH in Neu Wulmsdorf bei Hamburg ansässig und hat sich als Spezialist für hochwertige und maßgefertigte Holz-Metall-Fenster in verschiedensten Ausführungsvarianten in der ganzen Region einen Namen gemacht. Von der individuellen Beratung über die Planung bis zur Fertigung und Montage bietet das Unternehmen alle Leistungen aus einer Hand – ganz gleich, ob Einzelfenster oder Großprojekt, ob Neubau oder Sanierung. Besonders wichtig ist Geschäftsführer Jan Sehlmann und seinem Team die hohe Qualität. Das Unternehmen ist nach DIN ISO 9000 zertifiziert und fertigt strikt nach den RAL-Güterichtlinien.
https://sehlmann.de