Mit einer Produktionsfläche von 18 000 m2 und rund 200 Mitarbeitern ist die Produktion von Clarity Glass in São José dos Campos in vielerlei Hinsicht einzigartig. Die Produkte, hauptsächlich maßgefertigtes gehärtes Monoglas für den Innen- und Außenbereich, werden nur auf dem heimischen Markt im Umkreis von rund 600 km um Sao Paulo verkauft.
Die schiere Größe Brasiliens macht die Anlieferung des Glases zu einer Herausforderung. Früher war Clarity Glass mit 18 LKWs unterwegs, dann hat der Anbieter sein Vertriebsmodell umgestellt, um sich auf die Glasproduktion zu konzentrieren.
„Mein Geschäft ist B2B2B2C“, so Andre Costa, Eigentümer von Clarity Glass. „Wir arbeiten mit ca. 60 Händlern zusammen, die in der Nähe der örtlichen Glaser ansässig sind. Die Händler beliefern die Glasbetriebe nicht nur mit Glas, sondern auch mit allen anderen Materialien, die sie benötigen.“
Alle Vertriebspartner mit dem ERP-System verbunden
„Wir sind das letzte Glied in der Kette. Wenn der Kunde das Glas bestellt, ist das Gebäude schon fertig, und er möchte die Scheiben so schnell wie möglich haben.“ Um die Durchlaufzeiten zu verkürzen, hat Clarity Glass vor kurzem ein Projekt abgeschlossen, bei dem alle Vertriebspartner mit dem ERP-System verbunden wurden.
Die direkte Datenverbindung beschleunigt die Produktion, so Andre Costa: „Der Glaser zeigt dem Kunden das Produkt in einer App. Wenn der Kunde zustimmt, geht der Auftrag direkt in die Produktion. Wir brauchen weniger Zeit, und die Gefahr von Fehlern ist geringer.“ So kann Clarity Glass schnell maßgeschneiderte Produkte anbieten: innerhalb von 24 Stunden von der Jumbo-Scheibe zum Liefergestell, mit Lieferung an den Händler am nächsten Tag. Die Gesamtlieferzeit für den Kunden beträgt so nur 48 Stunden.
Von der manuellen zur vollautomatischen Fertigung
Als Clarity Glass 1996 gegründet wurde, wurden alle Arbeitsschritte manuell ausgeführt, während das Vorspannen ausgelagert war.
Andre Costa: „Als wir unseren ersten vertikalen Ofen kauften, arbeiteten wir in 3 Schichten, 7 Tage die Woche, und produzierten 5500 m² pro Monat. Jahr für Jahr haben wir neue Maschinen angeschafft und unsere Kapazität, unsere Erfahrung und unser Know-how ausgebaut. Heute wachsen wir mit der Unterstützung und dem Knowhow aus Österreich weiter.“
Clarity Glass besuchte Lisec (www.lisec.com) in 2017 in Österreich und erteilte 2018 den ersten einer Reihe von Aufträgen. „Wir waren auf der Suche nach einem Unternehmen, das die gesamte Lösung anbietet. Lisec ist der einzige Anbieter, den ich gesehen habe, der eine Komplettlösung für mein Vorhaben hatte.“
Viele Faktoren spielten bei der Wahl eine Rolle: „Lisec hat eine Menge Erfahrung, was für uns sehr wichtig ist. Wir wollten eine Geschäftsbeziehung mit einem Partner aufbauen, der über Erfahrung, Know-how, Problemlösung und ein gutes Ersatzteilnetzwerk verfügt.“ Für Andre Costa war es sehr wichtig, jeden Aspekt des Projekts zu verstehen: „Bevor wir mit der ersten Phase begannen, führten wir ausführliche Gespräche über das gesamte Projekt und die Lösung, einschließlich des Büros und aller Maschinen. Die Phasen waren darauf ausgelegt, die Funktionalität zu testen und einen sofortigen Return on Investment zu gewährleisten.“
Dank dieser sorgfältigen Vorbereitung konnten die Phasen 1 und 2 ohne größere Probleme oder Verzögerungen abgeschlossen werden.
In Phase 1 wurden ein Glaslagersystem mit einem Zuführkran (PKL), ein automatischer Schneidetisch (SprintCut) mit X-Brechung und ein kundenspezifisches Etikettiersystem installiert. „Wir haben drei manuelle Schneidetische durch einen automatischen Tisch ersetzt“, so Andre Costa.
In Phase 2 wurden die bestehenden Linien um eine automatische Y- und Z-Brechung und einen automatischen Transport (SHL) ergänzt.
Phase 3, die in 2024 und 2025 realisiert wird, umfasst ein automatisches Sortiersystem (ASM), das erste seiner Art in Brasilien. Es teilt den Produktionsfluss nach der Kantenbearbeitung auf.
Ein Teil fließt zu fünf topDRILL RX-Bearbeitungsanlagen von Schraml, von denen zwei mit einem Wasserstrahlschneidsystem ausgestattet sind.
Der zweite Fluss speist den Vorspannofen, wo die Scheiben in einer für das Härtebett optimierten Reihenfolge ankommen und von einem Roboterladesystem (RHH) be- und entladen werden. Clarity Glass ist das erste Werk mit automatischer Härtebettbeschickung in Lateinamerika.
Und die Software?
Im Hintergrund sorgt die Lisecs Produktionssoftware (GPS.prod) mit dynamischer Optimierung (Dynopt) für einen optimierten Zuschnitt sowie eine automatische Wiedereingliederung von Restscheiben. Das Lisec-Sortiersystem GPS.autofab mit dynamischer Pufferorganisation lenkt die Scheiben in die verschiedenen Produktionsströme. Am Vorspannofen sorgt die automatische Ofenbettoptimierung für eine möglichst platz- und energieeffiziente Auslastung. Weiter kontrollieren drei Viprotron ECO Qualitätsscanner die Qualität am Ende der Verarbeitungslinie.
Wenn er über seine Erfahrungen während des Projekts spricht, hebt Andre Costa die Zuverlässigkeit von Lisec hervor: „Die Zusammenarbeit ist professionell. Während ich in Österreich war, um das Projekt zu besprechen, wurden Spezialisten aus verschiedenen Bereichen gebeten, ihr Fachwissen einzubringen. Meiner Erfahrung nach kann es einen Punkt geben, an dem zu viele Anpassungen für einen Lieferanten zu komplex werden. Bei Lisec wurde alles schriftlich festgehalten. Als ich den Auftrag erhielt, umfasste er 110 Seiten – das gab mir Vertrauen. Man kann überprüfen, ob man genau das bekommt, wofür man bezahlt hat.“ Und Costa weiter: „Ich war jeden Tag in der Produktion, um den Fortschritt der Installation zu verfolgen, und alles war genau wie vereinbart, bis hin zur Anzahl der Bürsten in der Waschmaschine.“
Als technisch versierter Eigentümer, der früher selbst Glas in der Produktion bearbeitet hat, ist Andre Costa sehr an der Technologie hinter seinen Maschinen interessiert: „Wenn wir eine Maschine ein, zwei Jahre lang benutzen, können wir nicht anders, als nach Möglichkeiten zu suchen, sie zu verbessern – einen Sensor zu verschieben, ein Problem zu lösen. Wenn ich die Lisec-Maschinen ansehe, kann ich erkennen, dass Lisec das Gleiche tut. Lisec sucht immer nach Verbesserungsmöglichkeiten, mit dem eigenen Ingenieurteam, aber auch indem sie ihren Kunden zuhören. Ich schaue mir gerne bei Maschine die Details an. Bei den Lisec-Anlagen sehe ich Dinge, auf die ich nicht gekommen wäre. Ich bin mir sicher, dass Lisec viel in die Maschinenentwicklung und Marktforschung investiert.“
Zusammenfassend stellt Andre Costa fest: „Lisec bietet die besten Automatisierungs-Lösungen, die unsere Erwartungen erfüllen und jeden Tag, Jahr für Jahr, Stabilität gewährleisten. Ihre gut gebaute und zuverlässige Konstruktion ist für unseren 24-Stunden-Betrieb von entscheidender Bedeutung. Darüber hinaus ist es für uns sehr wichtig, den Lisec-Support in Österreich zu haben.“
Vision für die Zukunft
Auf dem hart umkämpften Markt in Brasilien hat Clarity Glass eine mutige Vision, so Andre Costa: „Wir wollen, dass der Endverbraucher die Marke Clarity direkt erkennt und nach ihr fragt, weil er das Clarity-Logo auf den Fenstern in seiner Wohnung und seinem Büro sieht.“
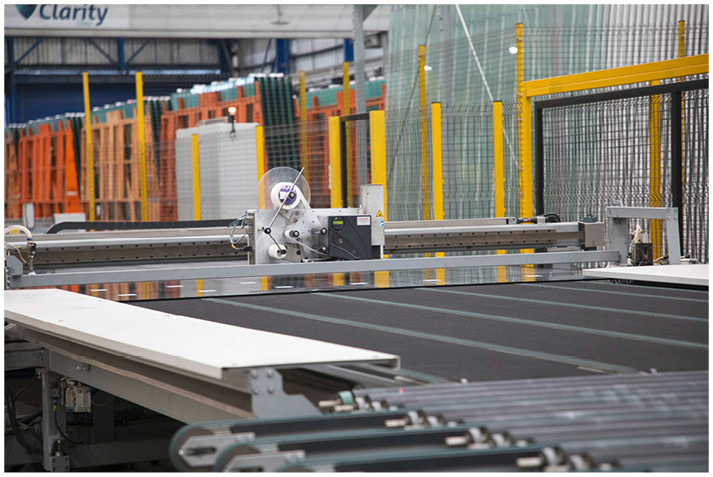
Foto: Clarity Glass
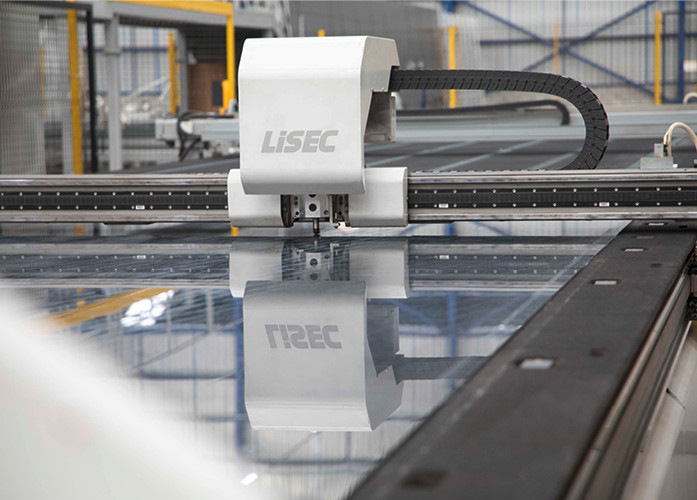
Foto: Clarity Glass
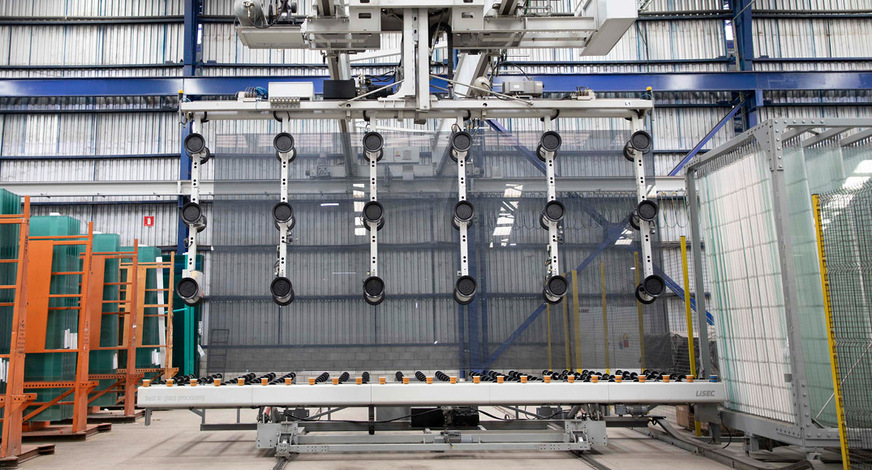
Foto: Clarity Glass
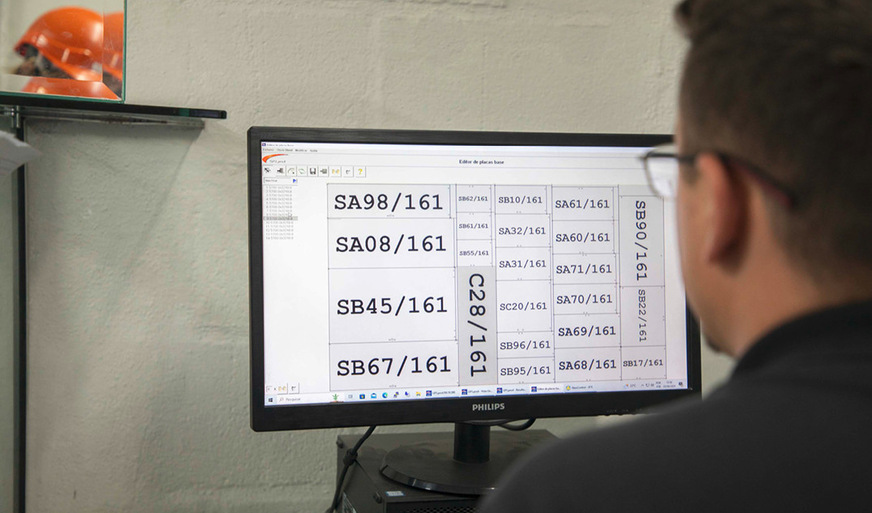
Foto: Clarity Glass
Nachhaltig produziert
Der Strom wird bei Clarity Glass hauptsächlich aus Solar- und Windenergie gewonnen, während die Glasabfälle direkt an einen nahe gelegenen Floatglashersteller zum Recycling weitergeleitet werden.
Außerdem wird das Wasser über ein Aufbereitungssystem wiederverwendet.