Verbundglaselemente aus Dünnglas: Dünnes chemisch gehärtetes Aluminosilikatglas wird häufig in der Elektronikindustrie für Displays verwendet. Eigenschaften wie hohe Festigkeit, Kratzfestigkeit, Stoßfestigkeit, optische Qualität sowie die geringe Dicke und das verminderte Gewicht machen die Verwendung hier besonders attraktiv, können aber auch in neuartigen Glasanwendungen nutzbar gemacht werden (Bild 01) [1] .
Insbesondere die sehr geringe Dicke von etwa 0,1 bis 2 mm und die hohe Biegefestigkeit von etwa 200 bis 1000 MPa [1] sind besonders hervorzuheben. Darüber lassen sich leicht gekrümmte Glaskonstruktionen mit kalt gebogenem Glas umsetzen. Zudem geht der Einsatz von Dünnglas mit einer deutlichen Gewichtsreduktion gegenüber herkömmlichen Fensterverglasungen einher.
Grundidee: Der schlichte Austausch von Fensterglas gegen Dünnglas ist aufgrund der hohen Flexibilität nicht möglich. Der Einsatz von Dünnglas ohne zusätzliche Maßnahmen führt zu hohen Verformungen, der Grenzzustand der Gebrauchstauglichkeit würde nicht eingehalten werden können. Außerdem können Schwingungen damit einhergehen. Aus Sicht von Betrachter und Nutzer ist beides nicht erwünscht.
Die Idee des Verbundglaselementes liegt darin, die Dünngläser durch einen inneren Kern aus geeigneten Kunststoffen auszusteifen, der im 3D-Druck hergestellt wurde.
Über eine lastabtragende Klebung, die den Kunststoffkern im Scheibenzwischenraum mit dem außenliegenden Glas koppeln, entsteht ein sehr leichtes und dennoch stabiles und tragfähiges Verbundelement. Für den Kunststoffkern werden Hohlkernmuster angestrebt, um den Kern zu optimieren im Hinblick auf eine weitere Gewichtsreduktion, auf die individuelle Gestaltbarkeit und eine größtmögliche Transparenz.
Das Kernmaterial kann opak aber auch lichtdurchlässig sein. Es kann architektonisch gestaltend eingesetzt oder aber auch zur Tageslichtlenkung herangezogen werden. (Bild 2)
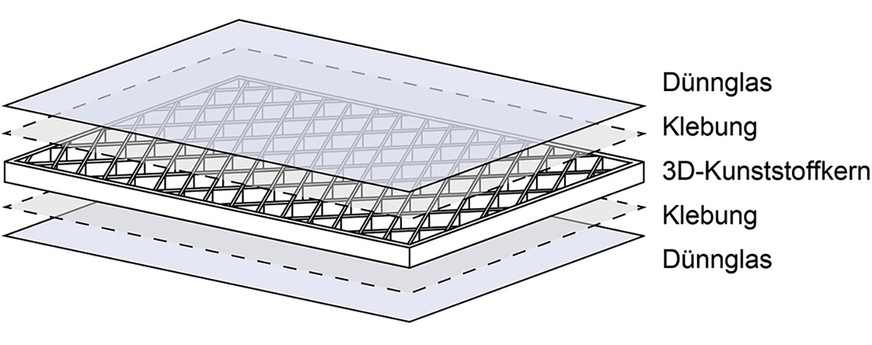
Foto: Institut für Baukonstruktion, TU Dresden
Muster des 3D-Kunststoffkerns
Mehrere Projektarbeiten untersuchten verschiedene Kernmuster. Dabei wurden die Verwendung von Hyparkern- und Fachwerkmustern sowie von Voronoi-Kernmustern näher betrachtet (Bild 3 und 4). Ein Hyparkernmuster erzeugt einen transluzenten, strukturierten 3D-gedruckten Kunststoffkern, der durch regelmäßige Perforation etwas an Durchsicht gewinnt. Ein fachwerkartiger Kunststoffkern wirkt dagegen transparenter und offener.
Im Rahmen einer Machbarkeitsstudie [2] wurden Verbundglaselemente in einer Größe von 210 × 297 mm hergestellt. Für die Außenscheiben des Verbundglaselementes wurden einzelne Scheiben aus chemisch gehärtetem Alumosilikat-Dünnglas der Dicke t = 0,7 mm verwendet. Der 11 mm dicke Kern wurde aus einem Polyethylenterephthalat-Glykol (PETG) modifiziertem Filament mittels Fused Deposition Modelling (FDM)-Technik gedruckt.
Aufgrund der Größenbeschränkung in der Drucktechnik wurde der Fachwerkkern in vier Teilen und der hyparförmige Kern in zwei Teilen gedruckt, die anschließend verklebt wurden. Um das Glas und den PETG-Kern sowie die einzelnen Teile des PETG-Kerns zu verkleben, wurde ein transparenter Zweikomponentenkleber auf Epoxidharzbasis gewählt.
Die kleinformatigen Paneele zeigten die architektonische Qualität sowie das Potenzial des Konzepts und erwiesen sich in einem 3-Punkt-Biegeversuch als sehr belastbar. Die Steifigkeit des Verbundes konnte auch rechnerisch bestätigt werden.
Eine weitere Studie [3] hatte zum Ziel, das Muster des Kerns weiter zu optimieren. Das Kernmaterial sollte nur dort verwendet werden, wo es strukturell am effizientesten ist, um gezielt Material und Gewicht zu sparen. Eine Parameterstudie untersuchte die Auswirkungen sich ändernder Randbedingungen im Hinblick auf die erforderliche Musterdichte.
![03: Verbundelement aus Dünnglas und 3D-gedrucktem Kern. Links im Bild ist ein hyparförmiger Kern zu sehen, rechts ein Fachwerkkern. [2]](/sites/default/files/styles/aurora_default/public/aurora/2020/03/25042.jpg?itok=GLdHUk0V)
Foto: MSc thesis Marina Guidi, TU Delft
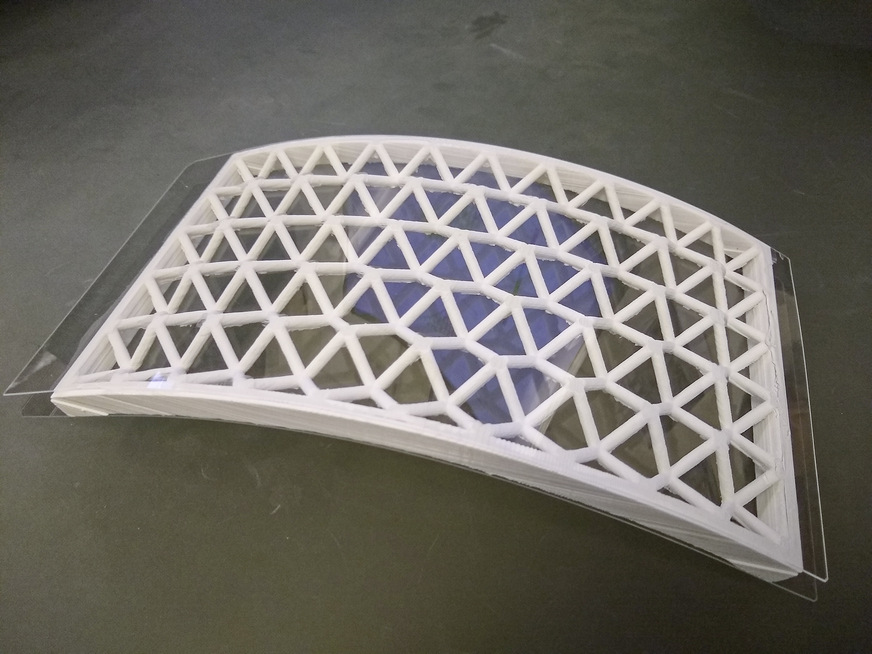
Foto: MSc thesis Marina Guidi, TU Delft
Der Aufbau der Prototypen
Um die Prinzipien und die praktische Umsetzbarkeit zu prüfen, wurden Glasverbundelemente in einer Größe von 150 × 300 mm hergestellt (Bild 4). Diese bestehen aus den 3D-gedruckten PETG-Kernen mit einer Nenndicke von t = 8 mm und zwei Außenschichten aus chemisch gehärtetem Alumosilikatglas mit einer Dicke von je t = 1 mm. Um das 3D-gedruckte Voronoi-Kernmuster mit den äußeren Glasschichten zu verbinden und einen gemeinschaftlichen Lastabtrag zu erzielen, wurden ein PET-Band mit Acrylklebeschicht und ein UV-härtender Acrylatklebstoff verwendet.
Die Prototypen veranschaulichten deutlich die architektonische Qualität des Verbundelements. Außerdem konnte auch für diese Elemente die Tragfähigkeit in einem 3-Punkt-Biegeversuch nachgewiesen werden. Es zeigte sich jedoch, dass insbesondere der Verbund zwischen den äußeren dünnen Glasscheiben und dem Polymerkern mithilfe des PET-Bandes nur unzureichend gewährleistet war. Die Klebung mit dem benannten Acrylatklebstoff erwies sich jedoch als sehr belastbar.
Mögliche Anwendungen
Obwohl die bisherigen Ergebnisse lediglich experimenteller Natur sind, erlauben sie dennoch einen vielversprechenden Blick in Zukunft. Es konnte in ersten Versuchen nachgewiesen werden, dass Verbundglaselemente aus Dünnglas und 3D-gedrucktem Kern äußerst tragfähig sind und gleichermaßen mit einem geringen Gewicht aufwarten. Sie werden damit deutlich montagefreundlicher als herkömmliche Verbundglasscheiben. Außerdem sind sie sehr gut als gekrümmte Struktur umsetzbar (Bild 5).
In ebener oder gekrümmter Form können sie im Innenbereich als Ausbauelement Verwendung finden, beispielsweise als Raumteiler oder Trennwand. Der 3D-gedruckte Kern ist nahezu frei gestaltbar, deshalb wird erwartet, dass das Verbundelement gerade für die Ausgestaltung der persönlichen Wohnwelt von hohem Wert ist. Eine Verwendung als Fassadenelement ist natürlich ebenso denkbar (Bild 1).
Für die Verwendung des Verbundelementes ist – je nach Anwendung – noch entsprechende Entwicklungsarbeit zu erbringen. Die umfassende Bewertung des Verbundverhaltens, der Nachweis der Tragfähigkeit und Dauerhaftigkeit der lastabtragenden Klebung und deren Herstellungstechnologie sowie die erforderliche Dichtigkeit des Randverbunds im Sinne eines vollwertigen Isolierglases sind nur einige wesentliche Fragen, die es noch zu klären gilt.
Im Rahmen aktueller Projektarbeiten an der TU Dresden werden derzeit weitere Kernstrukturen (Bild 6) und deren Klebbarkeit untersucht.
![05: Hier im Bild zwei Verbundglaselemente mit unterschiedlichen Kunststoffkernen im Voronoi-Muster.3]](/sites/default/files/styles/aurora_default/public/aurora/2020/03/25044.jpg?itok=Ihh5V5iA)
Foto: Institut für Baukonstruktion, TU Dresden
Die eingesetzten Materialien
Als Polymere für den 3D-Druck kamen PLA+, PETG und Green-TEC zum Einsatz. Aus einer Klebstoffrecherche und der Auswertung von Datenblattinformationen wurden in besonderem Hinblick auf Viskosität und Alterungsstabilität vier verschiedene Klebstoffe ausgewählt.
So sind Prüfkörper mit einem hochfesten 2K-Epoxidharz, mit einem flexibleren 2K-Polyurethan sowie mit zwei verschiedenen UV-härtenden Acrylaten hergestellt worden. Die wesentlichen Alterungseinflüsse in Fassadenanwendungen sind Temperaturwechsel und UV-Strahlung, so dass Klimawechselbeanspruchungen von -20 °C bis +80 °C und eine UV-Alterung durchgeführt wurden, um die Restfestigkeit nach Alterung zu ermitteln.
Die Zugfestigkeiten der 2K-Klebstoffe wurden durch die Alterungen nicht signifikant verändert. Die zunächst sehr hohen Festigkeiten der Acrylat-geklebten Prüfkörper fielen nach den Alterungen etwa auf das Niveau der 2K-Klebstoffe ab. Auffällig zeigte sich die 3D-gedruckte Struktur während der Alterungen durch die Einwirkung erhöhter Temperaturen. Hierbei trat starkes Verziehen des Materials auf, was unter Zugbeanspruchung häufig zu einem Substratbruch führte. [5]
Der nachfolgende Teil 2 beschreibt im nächsten Heft neue Konzepte zur Verwendung von Dünnglas als adaptive Fassadenelemente.
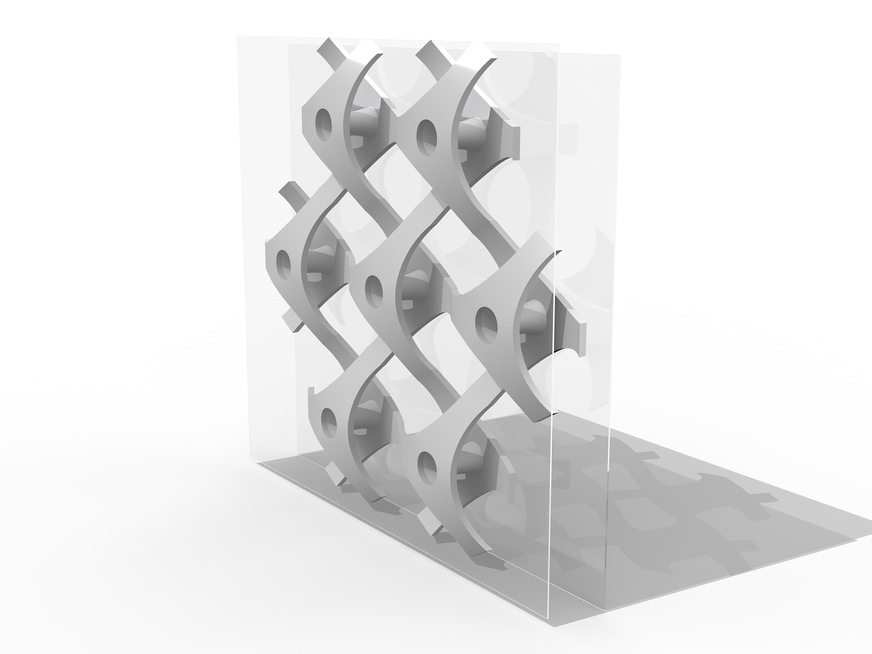
Foto: Daniel Pfarr, Institut für Baukonstruktion, TU Dresden