Jeder glasverarbeitende Betrieb hat eigene Anforderungen, die sich auch in Platzverhältnissen vor Ort oder unterschiedlichen Spezifikationen des Maschinenparks niederschlagen. Die Intralogistik, inklusive Puffer und Sortiersystemen, ist bei der Planung des optimalen Produktionsprozesse wesentliche Schlüsselelemente, und bieten die Möglichkeit, wesentliche Bearbeitungsschritte in der Wertschöpfungskette zu entkoppeln.
So kann die Intralogistik für weitgehende Prozessstabilität sorgen sowie die Versorgungssicherheit bei den jeweiligen Bearbeitungsschritten garantieren, auch bei unterschiedlichen Scheiben. Beispiel: Mit entsprechend abgestimmen Abläufen lassen sich beim optimierten Zuschnitt schon Scheibengrößen für spätere Produktionsläufe berücksichtigen, um die Glasplatte in erster Instanz optimal auszunutzen und Verschnitt zu vermeiden.
Die unterschiedlichen Scheiben werden im Puffer zwischengespeichert und können nach Abruf im jeweiligen Produktionslauf dann weiterverarbeitet werden, z. B. in der Isolierglas-Fertigung. So lassen sich die unterschiedlichen Produktionsprozesse nivellieren und glätten, und eine kontinuierliche Produktion am Laufen gehalten.
Puffer können zudem für den jeweiligen Betrieb maßgeschneidert angepasst werden, um einem optimal Materialfluss zu ermöglichen. So werden Einzelprozesse zu einem effizienten Werksfluss zusammengefasst.
Die Implementierung solcher Logistik-Systeme ist sowohl bei bestehenden Betrieben mit begrenzten Raumverhältnissen möglich als auch bei Green Field Projekten, die in ein hochautomatisiertes Puffer- bzw. Sortiersystem investieren möchten.
Auch die Integration von zugekauften Scheiben oder Remake-Scheiben ist bei hochqualitativen Intralogistik-Systemen möglich: Die Anschaffung eines derartiges Assistenzsystem hilft dem produzierenden Betrieb dabei Fehlbeladungen zu vermeiden sowie die Nachverfolgbarkeit der Scheiben sicherzustellen und Störungen auf den Produktionslinien zu verhindern. Das Ergebnis: verbesserte Performance bei steigender Qualität.
Intralogistik hebt die Qualität
Häufig wird bei der Flachglasverarbeitung bei der Intralogistik noch mit manuellen Lösungen gearbeitet, die neben Aspekten der Arbeitssicherheit auch eine erhöhte Fehlerquote bzw. hohe Auslastung bei Fachkräften mit sich bringt. Der Automatisierungsgrad neuerer Lösungen macht diese manuellen Eingriffe so gut wie obsolet und bringt noch andere Vorteile mit sich.
So wird beispielsweise nur die unbeschichtete Seite eines beschichteten Glases berührt und so die Beschichtung nicht beschädigt. Auch der Neigungswinkel von ca. 2° während des Transports der Scheibe dient dazu, die Beschichtung der Scheibe zu schützen.
Die Kantenqualität der Scheiben wird nicht beeinträchtigt. Ein weiterer Vorteil besteht in der Verfügbarkeit dieser Systeme, die hochautomatisiert 24/7 mit geringem Wartungsaufwand genutzt werden können. Lisec setzt bei derartigen Puffer- und Sortiersystemen beispielsweise auf hochwertige Führungsschienen, die gegen Glaspartikel geschützt sind.
Dadurch kann eine Laufleistung der industriellen Führungssysteme von ca. 1,6 Mio. km bei minimaler Wartung erreicht werden. Wie bereits anfangs am Beispiel des Zuschnitts erwähnt, kann die Intralogistik maßgeblich dazu beitragen, den Engpass des Zuschnittes aufzuheben und die jeweiligen Prozessschritte in der Produktion planbar und adäquat zu versorgen.
Generell gibt es eine hohe Vernetzungsvielfalt mit vor- und nachgeschalteten Prozessen, so können beispielsweise auch mehrere Zuschnittlinien miteinander verbunden werden.
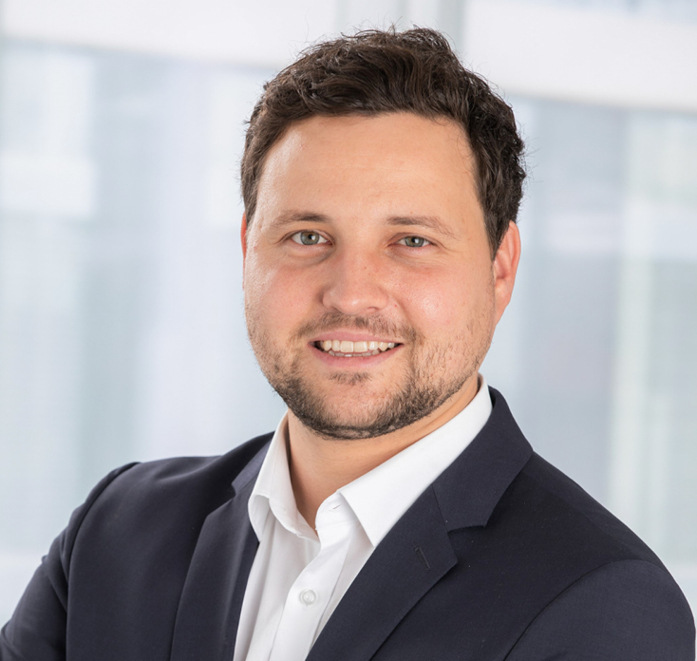
Foto: Lisec
Lisec Head of Product Management Logistics
Höhere Produktivität
Bei der Planung der Intralogistik ist der wesentlichste Faktor, die Kundenspezifika zu berücksichtigen. Der Werksfluss sowie der Produktmix müssen in die Planung des richtigen Puffer- bzw. Sortiersystems mit eingeplant werden.
Lisec bietet mit seinem Produktportfolio in Richtung Intralogistik ein breites Spektrum an und kann eine hohe Kombinatorik, die die unterschiedlichsten Anforderungen berücksichtigt, aber auch eine hohe Flexibilität hinsichtlich der Gläser (Sonderformen und Scheibengröße bis zu 6 × 3,3 m) anbieten.
Generell gilt aber bei der Frage, ob es Sinn macht mehrere Puffer einzusetzen: „so viel wie nötig, so wenig, wie möglich“.
Bei der Einzelscheiben-Sortierung macht eine Kaskadierung (mehrere Pufferstränge) von mehreren Puffer-Systemen, die mit einem gemeinsamen Shuttle Transport verbunden sind, durchaus Sinn. Hier werden in der ersten Pufferreihe die Scheiben gelagert, die zweite Pufferreihe optimiert und sortiert die Glasscheiben für die nachgeschalteten Prozessen.
Eine Mehrfachbeladung mit Scheiben je Speicherfach ist die Basis einer höheren Produktivität, da sie mit einer sehr hohen Lagerdichte bzw. einem hohen Füllgrad durch eine Bewegung mehrere Scheiben bewegbar und einsortierbar macht und zusätzlich sehr platzsparend ist.
Wohin gehen die Trends?
Ein derzeitiger Trend am Markt in die Isolierglas-Sortierung. Diese Entwicklung in Richtung der sicheren Aufbewahrung von Isolierglas-Elementen soll vor allem die Beladung der LKWs bzw. den Abtransport der Elemente optimieren bzw. erleichtern.
Die Rack-optimierte Produktion der Isolierglas-Elemente reduziert die benötigten Stellflächen und stellt eine Zeitersparnis durch die Beladung der LKWs in der richtigen Reihenfolge dar.
Zusammengefasst kann also gesagt werden, mit der richtigen Strategie kann und wird das richtige Puffer- bzw. Sortiersystem maßgeblich zum Erfolg des Betriebs beitragen: der Schlüssel dazu ist die Planung im Vorfeld, bei der man im Optimalfall auf das jahrelange Knowhow der Hersteller (z. B. Lisec) zurückgreift kann sowie deren Expertise bei der Umsetzung der jeweiligen Anforderungen innerhalb der automatisierten Lösung.
Weiter sollten neben der Hallenumgebung und dem Produktmix auch die im Betrieb verwendetet Glasgrößen, Glasdicken und Taktzeiten mit einberechnet werden, um eine High Performance Sortierung für die jeweiligen Kundenanforderungen anbieten zu können.
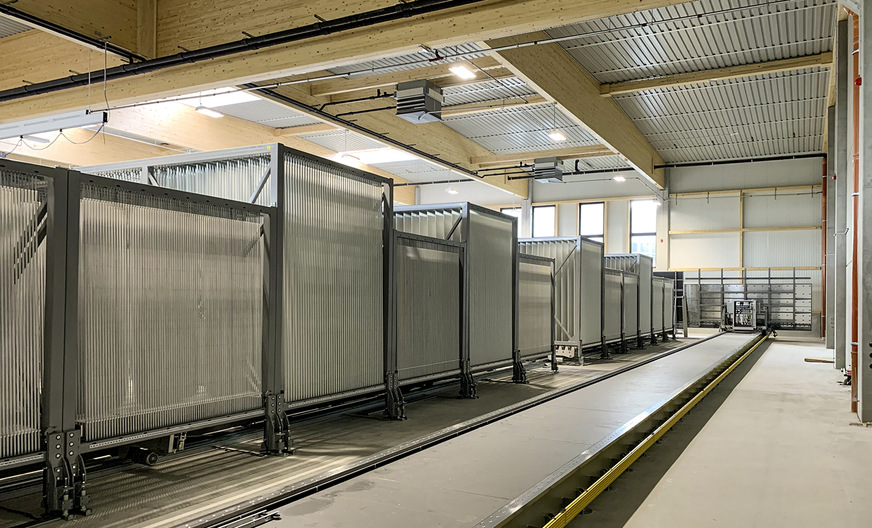
Foto: Lisec
Lisec Sorting-Solutions
Das leistet das Lisec-Puffer- und Sortierungssystem