Außergewöhnliche Fassadenkonzepte mit komplexen Geometrien und polygonalen Formen liegen mehr denn je im Trend. Vor diesem Hintergrund haben sich fünf Partner zusammengeschlossen, um gemeinsam einen komplett frei formbaren Fassadenknoten für Aluminiumprofilsysteme zu entwickeln, der sich natlos mit geraden Fassadenelementen kombinieren lässt.
Im Laufe der 1-stündigen Next Façade Session stellten die beteiligten Experten das gemeinsame Projekt vor und erläuterten dabei die technischen und gestalterischen Möglichkeiten von 3D-gedruckten Fassadenknoten.
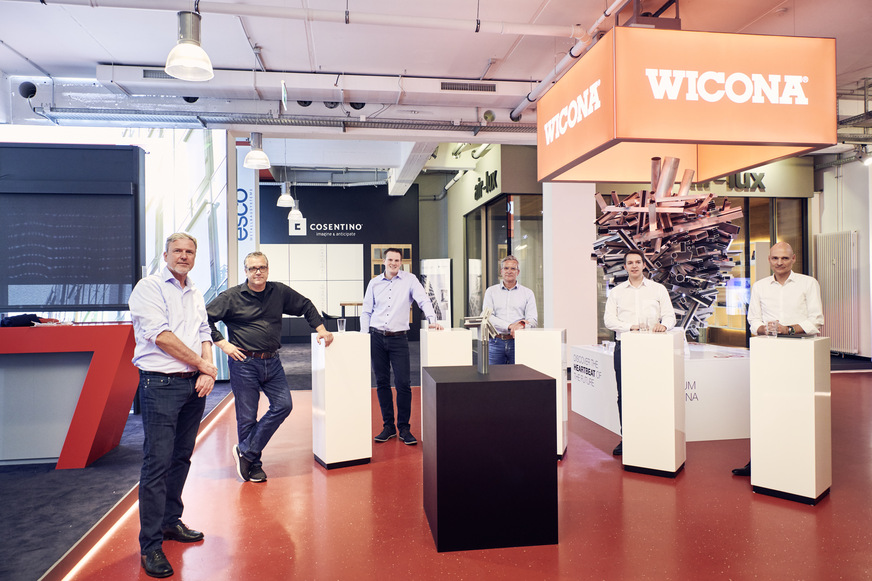
Wicona
Gleich zu Beginn machte Prof. Dr. Ulrich Knaack klar: „Unsere Entwicklung ist marktbereit. Mit unserer Lösung kann man alles realisieren, was krumm ist in der Fassade.“
Der monolithische Knoten diene als Verbindung gerader Verbindungselemente und ermögliche eine nahezu unbegrenzte Flexibilität der Konstruktion von Element- als auch Pfosten-/Riegel-Fassaden. Von klassisch rechtwinkligen über polygonale Geometrien bis hin zur kompletten Freiform sei alles machbar, so der 3D-Experte. Und zwar präzise, scharfkantig und ohne Schweißnähte. Nicht zuletzt eigne sich der Knoten auch als individuelles Gestaltungselement im Innenraum.
Prozesssicherheit auch bei komplexen Fassaden
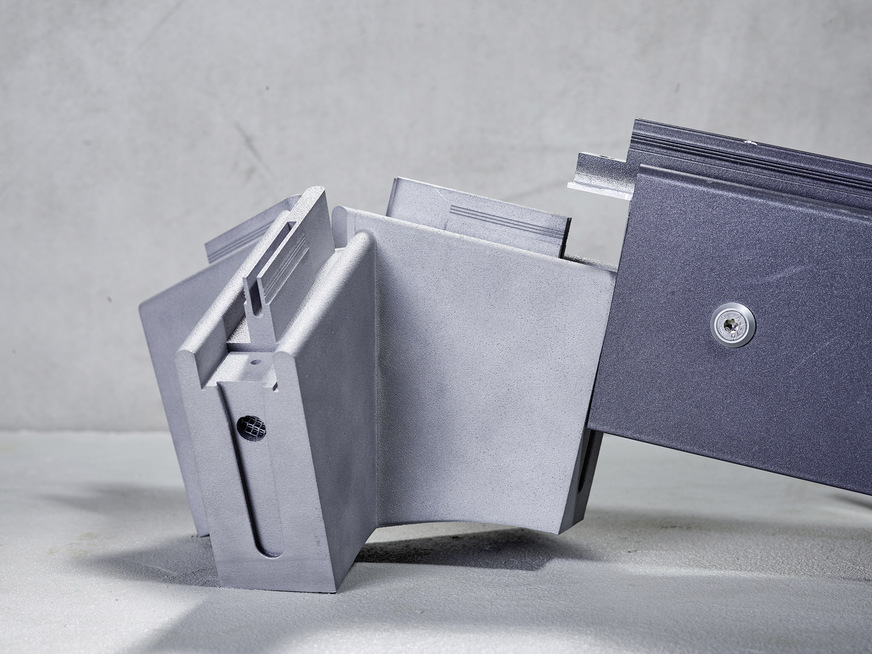
Wicona
Fassadenbauer wies Martin Rossmanith vor allem darauf hin, dass der Knoten eine hohe Prozess-Sicherheit und eine sehr gute handwerkliche Realisierbarkeit in der Montagepraxis biete. „Bisher mussten wir bei Freiformen Einschieblinge nutzen, Knoten schweißen und Profile sehr aufwändig zuschneiden.“ Die Bearbeitung sei mit dem neuen 3D-Knoten deutlich einfacher – die Profilbearbeitung beschränke sich auf einen einfachen Kappschnitt und die Verbindung erfolge fast wie bei den Bausätzen von „Fischertechnik“.
Damit sind technisch komplexe Herausforderungen sicher und mit hochwertiger Qualität umsetzbar – absolut verlässlich und reproduzierbar. Martin Rossmanith: „Das hilft Fassadenbauern, insbesondere im Hinblick auf den zunehmenden Zeit- und Kostendruck, sowie hinsichtlich des spürbaren Fachkräftemangels enorm.“
Als Experte für additive Fertigung und 3D-Druckverfahren hob Kai Kegelmann den intelligenten Ansatz des Knotenkonzepts hervor. „Das klassische Strangpressprofil kann bleiben und die komplette Komplexität wird in den Knoten überführt.“
Dazu komme, dass die Produktion mannlos und ohne Werkzeugvorbereitung läuft – direkt aus dem 3D-Modell auf die Maschine, skalierbar und immer in gleicher Qualität. Auch hinsichtlich der Materialwahl sei vieles möglich, so Kai Kegelmann: „Wir können alle schweißbaren Metalle drucken und erreichen im 3D-Druck sogar bessere Festigkeiten als bei klassischen Gussteilen.“
So lassen sich Standardprofile mit individuellen Formen umsetzen
Dr. Werner Jager (Wicona) führte aus, dass die Nachfrage nach 3-Dimensionalität im urbanen Raum immer mehr zunehme – aus gutem Grund: „Wir können mit 3D-Elementen nicht nur außergewöhnliche Formen realisieren, sondern auch Windlasten verteilen, Schall streuen und die Erhitzung von Fassaden reduzieren.“
Als System-hersteller sehe man mit dieser Innovation vor allem die Möglichkeit, bewährte Pfosten-Riegel- bzw. Aluminiumprofile mit komplett frei plan- und herstellbaren Fassadenknoten zu kombinieren und so noch individuellere Gebäudearchitekturen und Designvarianten zu ermöglichen.
Gefragt nach der bauaufsichtlichen Zulassung des marktreifen Systems, zeigten sich die Experten zuversichtlich. Derzeit seien ZiE beim DiBt notwendig, jedoch sei das System grundsätzlich nicht anders zu handhaben als Fassadenknoten aus Guss oder geschweißtem Metall. Somit müsse eine baldige bauaufsichtliche Zulassung durchaus machbar sein. Auch die Wirtschaftlichkeit sei gegeben – immer abhängig natürlich vom Projekt und der Komplexität der Fassadenlösung.
Zum Abschluss des Livestreams hatten die Zuschauer die Möglichkeit, per Chat Fragen direkt an die Expertenrunde zu stellen – was intensiv genutzt wurde. Weitere Informationen zu den Partnern und den 3D-gedruckten Fassadenknoten finden sich unter www.amvelope.com.
Die Spezialisten der Diskussionsrunde
Prof. Dr. Ulrich Knaack (TU Darmstadt, Institut für Statik und Konstruktion), der seine jahrelange Expertise in puncto 3D-Druck und additive Fertigungsverfahren mit einbrachte.
Martin Manegold von imagine computation erläuterte die digitalen Prozessen der Knoten-Generierung.
Kai Kegelmann von der Kegelmann Technik GmbH, ein versierter 3D-Druck-Experte, setzte mit seinem Team die modellierten Knoten mithilfe modernster Drucktechnik um.
Martin Rossmanith (Rossmanith Fenster + Fassade), ein etablierter Fassadenbauer, verwendete den Knoten bei einem aktuellen Projekt.
Werner Jager, Geschäftsführer Technisches Marketing von Wicona (www.wicona.de)