Das Fraunhofer IWM hat einen Prozess zum Glasbiegen entwickelt, um Glas in sehr engen Radien (z.B. 15 mm = 90° Biegewinkel) zu biegen und dabei gleichzeitig die optische Güte der Glasoberfläche von Floatglas beizubehalten.
Die gebogenen Glasscheiben, 2-fach- und 3-fach-Isolierglas sind möglich, können bestehende architektonische Lösungen ersetzen: Naheliegend ist z. B. eine Verwendung der Laser-gebogenen Scheiben als Glasecke von Gebäuden oder als Anwendung im Interieur, etwa für Duschen.
Durch den Einsatz einer gebogenen Isolierverglasung als Ecklösung entfällt zum einen das aufwendige Zusammensetzen der Glasscheiben an den Gebäudekanten als auch die damit verbundenen erhöhten Material- und Personalkosten. Gleichzeitig entfällt die sonst übliche „Wärmebrücke“ im Eckbereich, die sich dort durch die Verwendung von Abstandshaltern ergibt. Somit entstehen neben Kostenvorteilen auch positive Veränderungen für die energetische Bewertung eines Gebäudes sowie innerhalb des Produktlebenszyklus (Cradle-to-Cradle).
Die neue Formfreiheit erschließt vollkommen neue Anwendungsfelder für Glas. Gebogene Scheiben vereinen als Abdeckung technischer Produkte oder für Touchscreens eine Schutzfunktion mit modernen, funktionellen Designs.
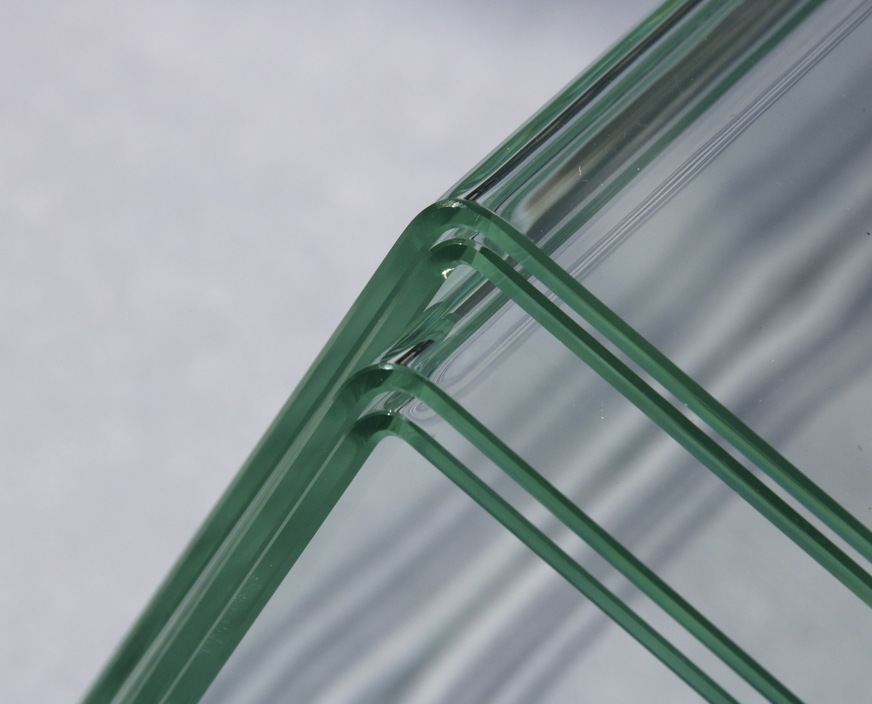
Bild: Peter Manns
Wo liegen die Unterschiede des neuen Fraunhofer-Biegeprozesses?
Durch das klassische Schwerkraftbiegen wären die angesprochenen Produkte nicht realisierbar. Zum einen würden die nicht gebogenen Bereiche durch das erweichte Glas auch an den Auflagepunkten etwas verformt (Einschränkungen bei der Optik), zum anderen wären solche extrem engen Radien von wenigen Millimetern nicht abbildbar. Der neue Ansatz am Fraunhofer IWM besteht darin, das Glas in lokal abgegrenzten Bereichen so weit zu erwärmen, dass es ausschließlich dort verformt werden kann.
Umgesetzt wird dies in einem am Fraunhofer IWM entwickelten Spezialofen. In diesem wird eine Scheibe gezielt auf den benötigten Temperaturbereich erwärmt. Unmittelbar im Anschluss zur globalen Erwärmung folgt die präzise lokale Erwärmung der zu biegenden Bereiche. Je nach Anforderung geschieht dies über einen Laser, Heizstrahler oder eine andere Strahlungsquelle.
Bei dem neuen Biegeprozess wird die Glasscheibe auf einer begrenzten Fläche erwärmt, wodurch das Glas dann lokal verformt werden kann, ohne an angrenzenden Bereichen ebenfalls eine (unerwünschte) Verformung zu bewirken. Mit dieser Technik werden die Scheiben quasi geknickt. Ein solcher Knick lässt sich an mehreren Abschnitten einer Scheibe einbringen.
Was sind die Vorteile des neuen Verfahrens?
Im Rahmen der der Entwicklungsarbeiten wurde der Prozess weiter verbessert und auf neue Anwendungsfälle übertragen. Zum einen wurden an verschiedenen Glasarten und –dicken erfolgreiche Biegeversuche durchgeführt, zum anderen wurden Parameter wie Biegegenauigkeit und Prozesszeit weiter optimiert.
An dieser Stelle setzt nun die „Künstliche Intelligenz“ (AI) an, in Form eines Programms zum maschinellen Lernen („Machine Learning“). Die durch das neue Verfahren erweiterte Designfreiheit erfordert für unterschiedliche Geometrien angepasste Temperaturverläufe. Die Temperaturen in der Ofenkammer und auf dem Glas werden über Thermo-Elemente im Sekundentakt in eine Datenbank geschrieben.
Auf diese Daten – sowie auf über 20 weitere Sensor-Daten – greift das implementierte „Machine Learning Modell“ zu (als Teil von AI) und berechnet bei Erreichen einer sogenannten Triggertemperatur eine Wahrscheinlichkeitsverteilung aus einer Auswahl von Laserprogrammen.
Diese stellt wiederum das Ranking der Laserprogramme zur Erwärmung der Biegefläche dar, mit denen Ziel-Radius und -Biegewinkel am ehesten erreicht werden und hilft somit bei der Auswahl des optimalen Programms für die entsprechende Geometrie.
Angesichts individueller Geometrien können so Entwicklungszeiten verkürzt werden und im industriellen Umfeld lässt sich so eine kürzere Time-to-Market realisieren.
Aktuell erfolgt die Erstellung, Anpassung und Auswahl des Laserprogramms noch manuell, doch Ziel ist es, dass die selbst-lernenden Modelle direkt Einfluss auf Maschinensteuerung und -regelung nehmen (siehe Grafik).
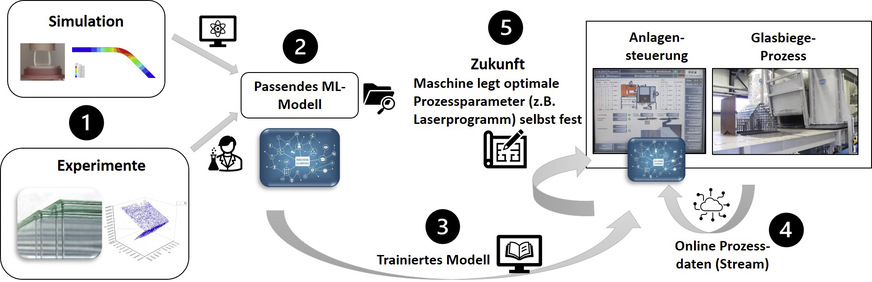
Bild: Fraunhofer IWM