Außergewöhnliche Fassadenkonzepte mit komplexen Geometrien und polygonalen Formen liegen im Trend. Vor diesem Hintergrund haben sich fünf Partner zusammengeschlossen, um gemeinsam einen komplett frei formbaren Fassadenknoten für Aluminiumprofilsysteme zu entwickeln, der sich nahtlos mit geraden Fassadenelementen kombinieren lässt.
Im Laufe einer 1-stündigen Façade Session aus dem Next Studio stellten die beteiligten Experten das gemeinsame Projekt vor und erläuterten die Möglichkeiten von 3D-gedruckten Knoten.
Gleich zu Beginn machte Prof. Dr. Ulrich Knaack klar: „Der von uns entwickelte Knoten ist marktbereit. Damit lässt sich alles realisieren, was krumm ist in der Fassade.“
Der monolithische Knoten ermögliche eine fast unbegrenzte Flexibilität der Konstruktion von Element- sowie von Pfosten-/Riegel-Fassaden. Von rechtwinkligen über polygonale Geometrien bis hin zur kompletten Freiform sei alles machbar: präzise, scharfkantig, ganz ohne Schweißnähte. .
Mehr Sicherheit für Metallbauer
Fassadenbauer Martin Rossmanith wies darauf hin, dass der 3D-Knoten eine hohe Prozess-Sicherheit und eine sehr gute handwerkliche Handhabe bei der Montage biete. „Bisher mussten wir bei Freiformen Einschieblinge nutzen, Knoten schweißen und Profile aufwändig zuschneiden.“ Mit dem neuen 3D-Knoten sei alles deutlich einfacher: Die Profilbearbeitung beschränke sich auf einen einfachen Kappschnitt und die Verbindung erfolge fast wie bei den Bausätzen von „Fischertechnik“, so der Metallbauer.
Und weiter: „Das hilft uns enorm, gerade im Hinblick auf den steigenden Zeit- und Kostendruck, sowie in Bezug auf den Fachkräftemangel.“
Als Experte für additive Fertigung und 3D-Druck hob Kai Kegelmann den intelligenten Ansatz des Knotenkonzepts hervor. „Das klassische Strangpressprofil kann bleiben und die Komplexität wird in den Knoten überführt.“ Im Bezug auf die Materialwahl sei vieles möglich, so Kegelmann: „Wir können alle schweißbaren Metalle drucken und erreichen im 3D-Druck sogar bessere Festigkeiten als bei klassischen Gussteilen.“
Dr. Werner Jager (Wicona) ergänzt: „Wir können mit 3D-Elementen nicht nur besondere Formen realisieren, sondern auch Windlasten verteilen, Schall streuen und die Erhitzung von Fassaden reduzieren.“ Als Systemhersteller sehe er mit der Innovation die große Chance, bewährte Pfosten-Riegel- bzw. Aluprofile mit komplett frei plan- und herstellbaren Fassadenknoten zu kombinieren und so noch individuellere Gebäudearchitekturen und Designvarianten zu ermöglichen.
Gefragt nach der bauaufsichtlichen Zulassung des marktreifen Systems, zeigten sich die Experten zuversichtlich. Derzeit seien ZiE beim DiBt nötig, jedoch sei das System nicht anders zu handhaben als Fassadenknoten aus Guss oder geschweißtem Metall. Somit rechne man mit einer baldige bauaufsichtliche Zulassung.
Zudem sei die Wirtschaftlichkeit gegeben – immer abhängig natürlich von dem jeweiligen Projekt sowie der Komplexität der gewünschten Fassadenlösung.
www.wicona.com | www.next-studio.de
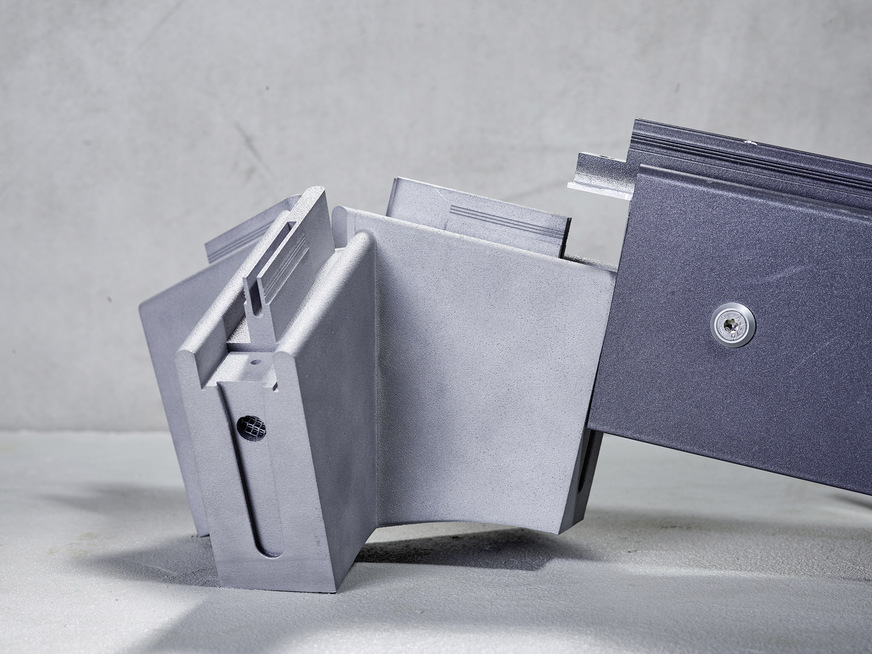
Foto: Wicona