Diese Investition ist die größte in der Firmengeschichte und Teil eines umfassenden 10-Mio.-Euro-Modernisierungspakets, das neben der Fertigungslinie auch einen neuen Kran, eine zusätzliche Anbauhalle sowie ein modernes Sozialgebäude inklusive neuer Ausstellung für Mitarbeiter und Besucher umfasst. Mit der neuen ‚Super Heroes‘-Anlage wird Produzent Niveau selbst zum echten Superhelden unter den Holzfensteranbietern. Außerdem markiert die Anlageninvestition einen Wendepunkt in der Verbindungstechnik. Denn der Produzent verabschiedet sich vom Schlitzzapfen und führt den Konterdübel ein, die Verbindung der Zukunft, die laut Prokurist und Fertigungs-Mastermind Andreas Malter „die einzige Holzverbindung ist, die man auch industrialisieren kann“.
Was kann Working Process, was andere nicht können?
Auf der Suche nach einer neuen Hochleistungsanlage für die Fensterproduktion hat Niveau verschiedene Anbieter unter die Lupe genommen. Die Wahl fiel schließlich auf den italienischen Maschinenbauer Working Process (WP), der sich als Spezialist für leistungsstarke Fensterbaumaschinen einen Namen gemacht hat. „WP und insbesondere Geschäftsführer Massimo Schiavetta ist für uns der Impulsgeber, wenn es um Spitzenleistungen in der Fensterproduktion geht“, erklärt Niveau-GF Dieter Heep. Der Besuch im WP-Werk in Italien hat bei ihm einen bleibenden Eindruck hinterlassen. Der Maschinenbauer hat seine Produktionsfläche in den letzten Jahren verdoppelt – ein starkes Zeichen für den Erfolg.
Besonders beeindruckt zeigte sich das Niveau-Team vom Maschinenkonzept: „WP baut Anlagen für hohe Leistungen. Da diskutiert man nicht über den Sonderbau.“ Stattdessen setzt der Hersteller auf Modulbauweise, die sich flexibel an die Anforderungen anpassen lässt.
Die Qualität des Maschinenbaus war ein wichtiger Entscheidungsfaktor. Die schweren Spannkonsolen, die WP in allen Baureihen einsetzt, sorgen für einen ruhigen Lauf und ein exzellentes Fräsbild. Auch die Sauberkeit der Bearbeitungszelle überzeugte: „WP hat sich Gedanken gemacht, wie die Späne vom Werkstück wegkommen. Das ist in der Anlage deutlich durchdachter als bei anderen Systemen.“ Zudem verbaut der italienische Anlagenbauer ausschließlich hochwertige Komponenten. Von der Pneumatik von Festo über die Steuerung von Siemens (durch Updates wird die Anlagensteuerung immer schneller und effizienter) bis hin zu erstklassigen Spindeln.
Werkzeugauswahl passt zum Konzept
Besonderes Augenmerk legte Niveau auf das Werkzeugkonzept: „Wir haben die Bearbeitungsschritte sinnvoll gesplittet, um schonend zu arbeiten und den Werkzeugeinsatz zu optimieren“, so Malter. Dabei hätten die Werkzeuge von TWT Zuani im direkten Wettbewerbsvergleich überzeugt. Hier bestand der Holzfensterproduzent auf einer speziellen Beschichtung der Werkzeugkörper, die bisher nicht zum Angebot von TWT gehörte. Das wurde akzeptiert - und inzwischen bietet Zuani diese Beschichtung sogar erfolgreich anderen Kunden an.
Die neue Anlage ist seit kurzem in Betrieb, die ersten Erfahrungen sind durchweg positiv. Insgesamt zeigt sich das Niveau-Team rund um Familie Heep sehr zufrieden mit seinen Sparringspartnern in Sachen Anlagenbau, Werkzeug und Software: Auch die Zusammenarbeit mit dem Softwarehaus 3E, das für die Datenaufbereitung zuständig ist, funktioniere reibungslos. „Ohne Daten keine Teile“, bringt es Heep auf den Punkt. Entscheidend für den Projekterfolg sei die hervorragende Unterstützung aller Partner gewesen.
Die Beleimtechnik neu erfunden
Die eingangs erwähnte Entscheidung, die Verbindungstechnik zu wechseln, bringt klare Vorteile: höchste Präzision vom Einzelteil bis zum fertigen Rahmen sowie einen deutlich schnellerer Durchsatz. In Zusammenarbeit mit dem Maschinenhersteller Koch hat Niveau unter Mitwirkung des Beratungshauses Tre Innova aus der Schweiz (Heep: „Linus Oehen von Tre Innova markierte hier den wichtigen Dreh- und Angelpunkt“) die bestehende Dübel- und Beleimtechnik weiterentwickelt und leistungsfähiger konzipiert. Ein klarer Fortschritt: Der automatisierte Leimauftrag ersetzt die manuelle Arbeit. „Wir verabschieden uns von diesen unsauberen Leimarbeitsplätzen“, freut sich Malter. Das bedeutet nicht nur mehr Sauberkeit, sondern auch eine höhere Produktqualität ohne Leimflecken auf lasierten Fenstern. Gleichzeitig werden drei Arbeitskräfte für andere Aufgaben frei.
Intelligente Fertigungssteuerung
Die WP-Anlage selbst beeindruckt durch ihre Selbstoptimierung. Sie ermittelt eigenständig die beste Belegung der Bearbeitungsstationen und entscheidet, wie die kürzeste Gesamtdurchlaufzeit erreicht werden kann. Malter: „Die Anlage checkt selbst, wie sie schneller arbeiten kann,“ meist werden drei bis vier Teile pro Bearbeitungsstation belegt, um auf allen vier Linien die beste Balance zu erzielen. Besonderes Augenmerk wurde auf die Spannqualität gelegt. Es gibt mehr und größere Spannzangen, die für weniger Spanndruck und höhere Präzision sorgen.
Ein wesentlicher Leistungsfaktor ist die Entkopplung des Hobelprozesses von der CNC-Bearbeitung. Die Hobellinie arbeitet etwa doppelt so schnell wie die CNC-Zelle und kann von einer Person bedient werden. Ein intelligentes Materiallogistiksystem (IMML) sorgt für die optimale Pufferung und Bereitstellung der Teile.
„Wir können verschnittoptimiert hobeln, weil wir durch diese Entkopplung den gesamten Zuschnitt- und Hobelprozess mit der Zuschnittoptimierung materialschonend gestalten“, geht Malter ins Detail. Das IMML-System sortiert die Teile und bedient die CNC-Bearbeitung optimal. Die Pufferfunktion ermöglicht es, Teile mit gleicher Länge, gleicher Holzart und gleichem Querschnitt übereinander zu stapeln. Während die eine Hälfte des Systems die CNC-Zelle beschickt, übernimmt die andere Hälfte die Teile von der Hobellinie. Diese parallele Arbeitsweise ist einer der Schlüssel für die hohe Leistungfähigkeit der Anlage. Technologisch positioniert sich der Fensterhersteller damit an der Spitze der Branche.
Woher kommt das Wachstum?
Der Holzfensterhersteller verzeichnete in den ersten beiden Monaten dieses Jahres ein Umsatzplus von 10 Prozent gegenüber dem Vorjahreszeitraum, was Wachstum auch in schwierigen Marktphasen demonstriert und die Investitionen rechtfertigt. Seit 2018 konnte das Unternehmen jedes Jahr meist zweistellig zulegen, trotz einer investitionsbedingten Umsatzreduktion im letzten Jahr, bei der die Produktivität dennoch um 3 Prozent stieg. Dieter Heep hebt die Bedeutung der breiten Aufstellung hervor: „Wir können beides – Einzelanfertigungen und Großserien.“ Diese Flexibilität ist ein entscheidender Vorteil.
Das Unternehmen ist in drei Geschäftsfeldern tätig: Händlergeschäft (65 Prozent), Fertighausbau (25 Prozent) und Objektgeschäft (10 Prozent), wobei die Anteile seit Jahren konstant sind.
Das sind die Wachstumstreiber
Vor allem das Objektgeschäft hat sich in der aktuellen Baukrise als wichtiges Standbein erwiesen: „Wir haben mehr Anfragen, als wir bearbeiten können“, freut sich Heep. Der Radius für Objektprojekte liege in der Regel bei 150 bis 200 km, für lukrative Aufträge fahre man aber dennoch nach Hamburg oder München. Möglich macht das ein Netzwerk leistungsfähiger Handelspartner, die die Montage übernehmen können.
Auch das Segment Denkmalschutz trägt wesentlich zum Erfolg bei. Referenzprojekte wie die Aachener Jahrhunderthalle mit tausenden Einzelfenstern unterstreichen die Kompetenz in diesem anspruchsvollen Thema.
Im Fertighausbereich konzentriert sich Niveau auf Partner im Premiumsegment (Stommelhaus, Weberhaus, Huf-Haus), die von der allgemeinen Neubaukrise kaum betroffen sind.
Nicht zuletzt sorgen auch die Handelspartner für gute Umsätze. Sie werden intensiv unterstützt, insbesondere diejenigen, die in ihre Ausstellungen investieren. „Wir arbeiten kundenorientiert und konsequent partnerschaftlich.“ Diese Strategie zahlt sich durch treue Händler aus, die auch in schwierigen Zeiten für kontinuierliche Aufträge sorgen.
Die Kombination aus technologischer Innovation, Produktvielfalt und strategischer Marktbearbeitung erweist sich als Erfolgsformel, mit der das Unternehmen auch in herausfordernden Zeiten wachsen kann.
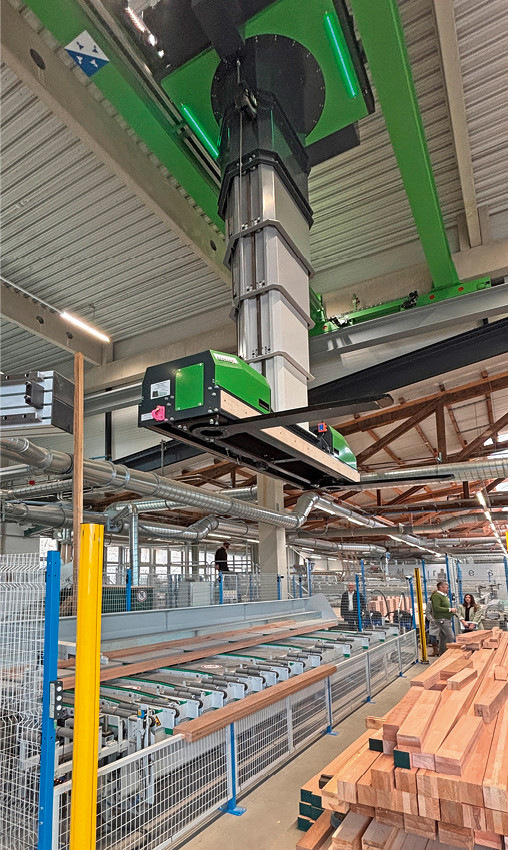
Foto: Daniel Mund / GW
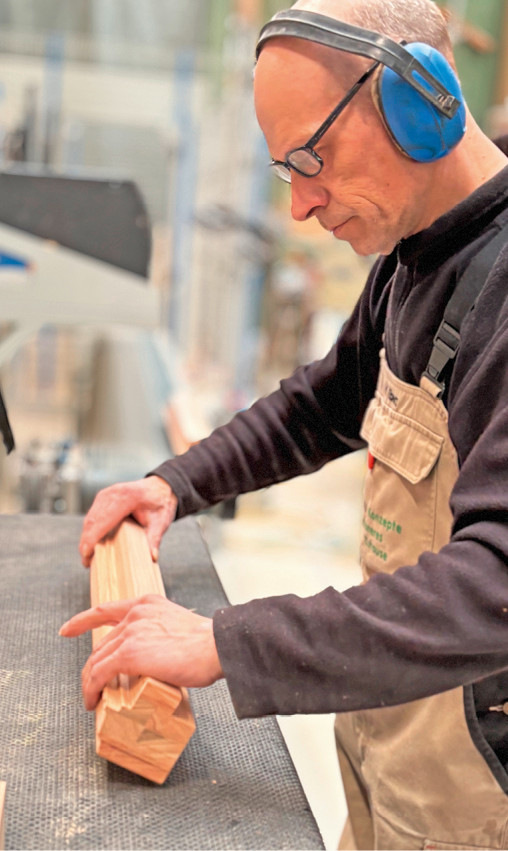
Foto: Daniel Mund / GW
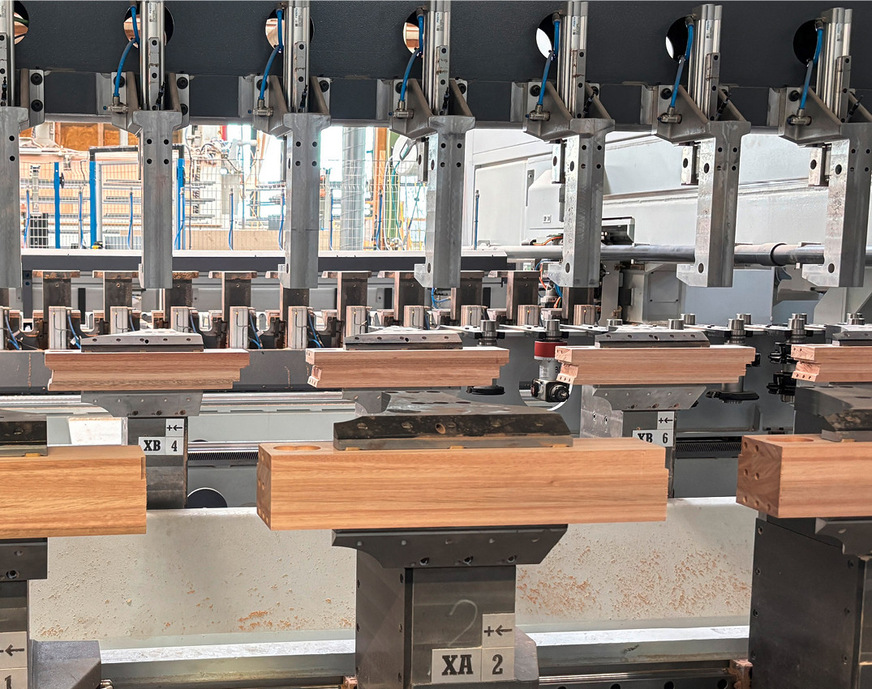
Foto: Daniel Mund / GW
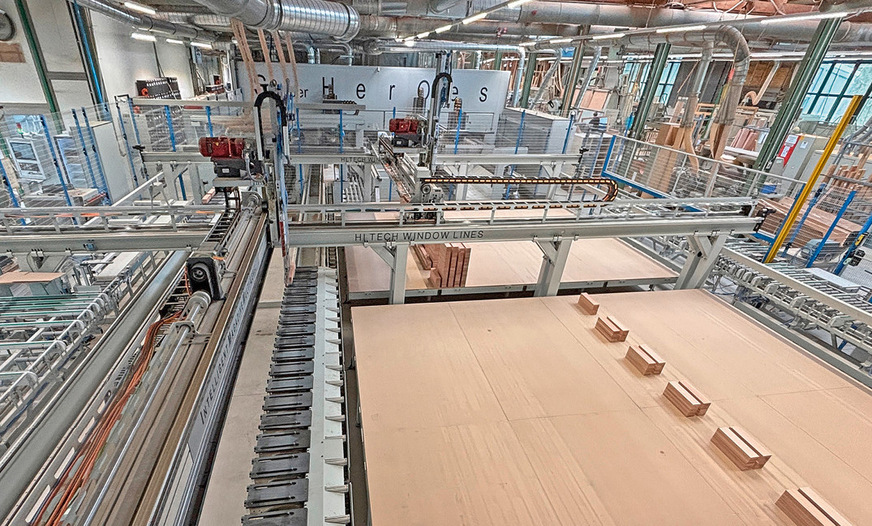
Foto: Daniel Mund / GW
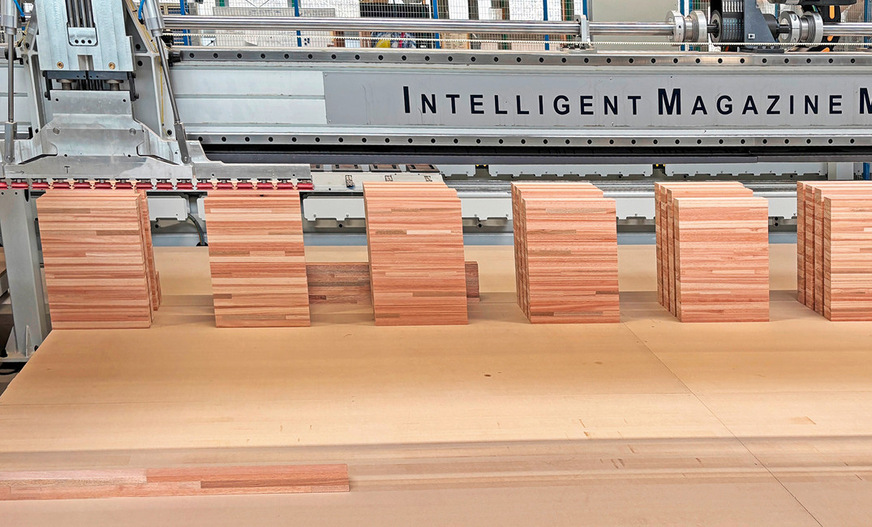
Foto: Daniel Mund / GW
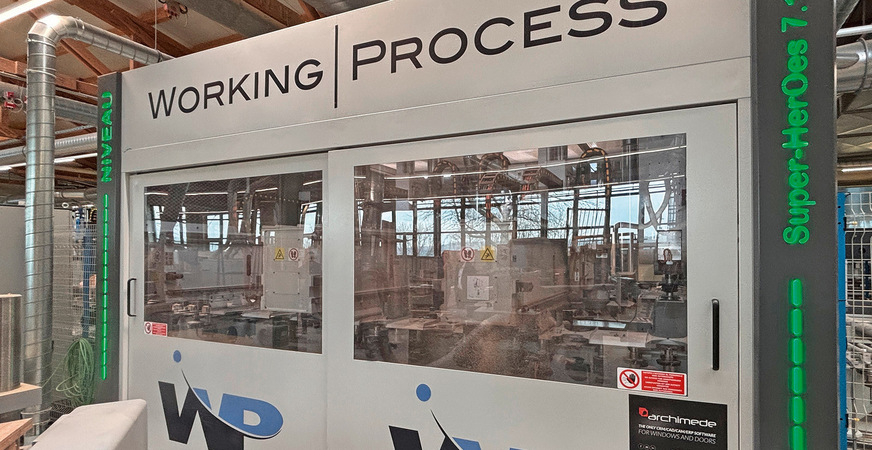
Foto: Daniel Mund / GW
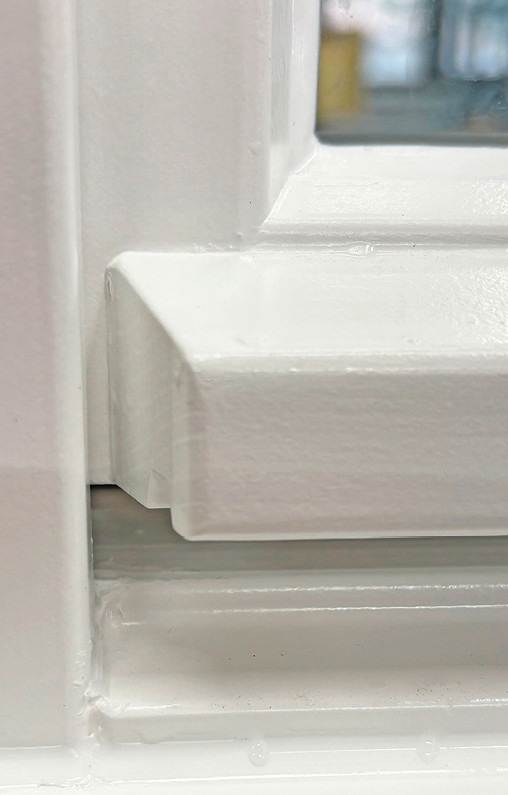
Foto: Daniel Mund / GW
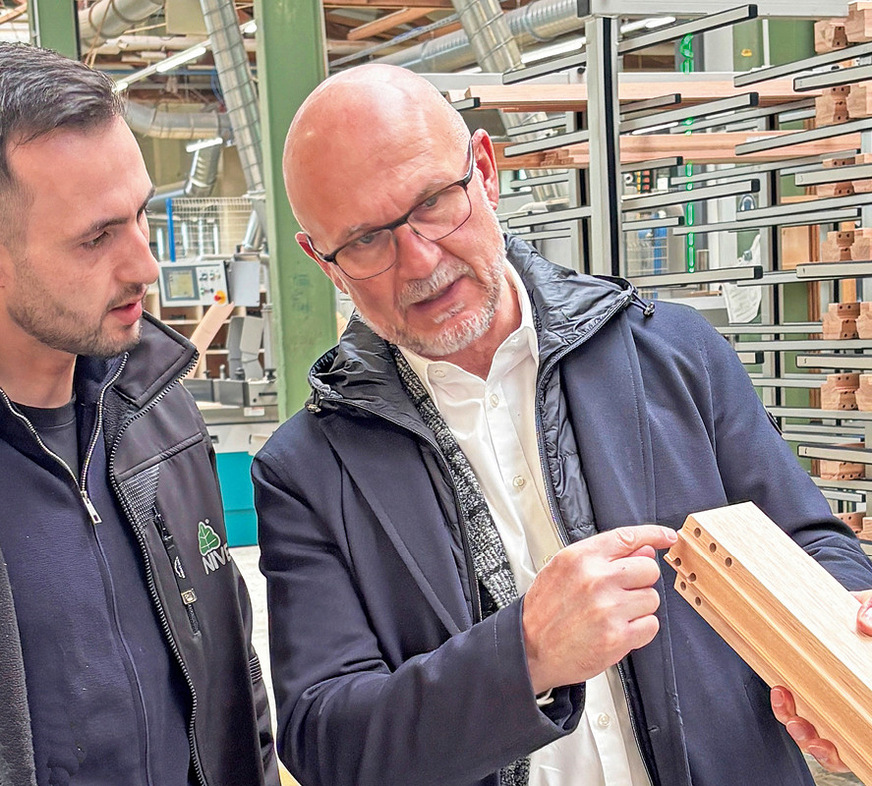
Foto: Daniel Mund / GW
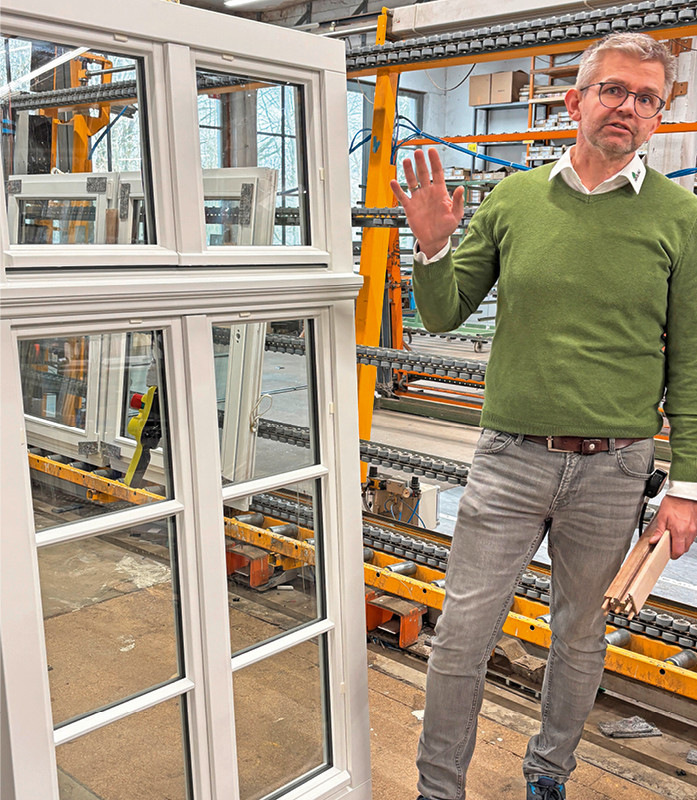
Foto: Daniel Mund / GW
So tickt Niveau Fenster
Die Niveau Fenster Westerburg GmbH ist ein renommierter Hersteller von Fenstern und Türen aus Holz und Holz-Aluminium mit Sitz in Westerburg bei Montabaur (Jahresumsatz deutlich über 20 Mio. Euro, 140 Mitarbeitern). Das 1959 gegründete Unternehmen verbindet modernste Fertigungstechnologien mit traditioneller handwerklicher Holzverarbeitung zu maßgeschneiderten Bauelementen.
Die Geschäftsführung besteht aus Dieter Heep. Prokuristen sind Max Heep (IT und Organisation) und Andreas Malter sowie Claudia Stevens.
Niveau bietet klassische und moderne Holzfenster, Holz-Aluminium-Fenster sowie individuelle Haustüren aus Holz. Die Produkte zeichnen sich durch hochwertige Materialien, exzellente Verarbeitung und vielfältige Anpassungsmöglichkeiten aus, die es Kunden ermöglichen, ihre persönlichen Vorstellungen zu verwirklichen.
Mit Lösungen wie dem neuen Holz-Aluminium-Fenster in Fichte Altholz, das Nachhaltigkeit mit einer einzigartigen natürlichen Optik verbindet, setzt Niveau Maßstäbe in der Branche.
Niveau legt großen Wert auf Qualität und Nachhaltigkeit. Das Unternehmen ist Träger des RAL-Gütezeichens für Fenster und Haustüren. Außerdem setzt Niveau auf Hölzer aus nachhaltiger Forstwirtschaft und umweltfreundliche Produktionsmethoden.
Die Zugehörigkeit zur Heep-Gruppe ermöglicht eine enge Zusammenarbeit im Vertrieb und die Nutzung von Synergien, beispielsweise in den Bereichen Logistik, Einkauf und IT.
Interview mit Michael Hemmerich, Working Process Deutschland
GW– Herr Hemmerich, Sie haben die neue Niveau-Anlage realisiert. Wie kam es zur Zusammenarbeit?
Michael Hemmerich– Niveau hatte den Wunsch, die Produktionsprozesse grundlegend zu erneuern – und das nicht nur mit Blick auf Maschinen, sondern auf das gesamte Konzept. Wir wurden eingeladen, unsere Lösung vorzustellen. Was folgte, war ein intensiver Prozess über 15 Monate, von der ersten Idee bis zur finalen Entscheidung.
GW – Was gab den Ausschlag zugunsten von WP?
Hemmerich – Der Mut von Niveau, sich auf ein Hochleistungs-CNC-Konzept einzulassen – und unsere Fähigkeit, die passende technische Lösung zu liefern. Ein Schlüsselfaktor ist der sogenannte IMML-Puffer, der eine hochflexible Teilelogistik ermöglicht. Anders als bei klassischer rahmenweiser Fertigung, bei der ein kompletter Flügel in einer Linie bearbeitet wird, setzen wir auf die Optimierung jedes einzelnen Bearbeitungsschritts. Der Puffer kann je nach Auslegung zwischen 100 und 600 Teile aufnehmen. Das reduziert Umrüstzeiten drastisch und schafft enorme Flexibilität. So entsteht deutlich mehr Effizienz – mit dem Effekt, dass beispielsweise der Hobel nur noch etwa 50 Prozent der Zeit läuft und der Rest der Zeit für andere Aufgaben genutzt werden kann.
GW – Warum keine rahmenweise Fertigung?
Hemmerich – Wir sehen darin den entscheidenden Effizienznachteil. Rahmensysteme sind zwar in der Logistik einfacher, verschenken aber oft Produktionsfläche und blockieren Maschinen durch häufige Werkzeugwechsel. Bei uns wird jeder Prozess für sich optimiert – und durch ein Labelsystem ist die spätere Teilezuordnung trotzdem sauber gelöst. Wir verfolgen das Prinzip: erst maximale Ausnutzung der Maschinen – dann Sortierung und Zusammenstellung.
GW – Was steckt sonst noch in der Anlage?
Hemmerich – Die Anlage kombiniert mehrere Bearbeitungsstationen: zunächst die Querbearbeitung mit vorgelagerter Kappsäge, Bohrmaschine und IMML-Puffer. Das Entscheidende: Das Werkstück wird nur einmal aufgenommen und durchläuft alle Bearbeitungsphasen ohne neuerliches Referenzieren. Dadurch entstehen hohe Präzision und weniger Verschleiß.
GW – Und wie lief die Umsetzung hier konkret ab?
Hemmerich – Im September haben wir die Vorabnahme in Italien gemacht, im Oktober wurde die Anlage bei Niveau installiert – parallel zum laufenden Betrieb. Dank guter Vorbereitung konnten wir schnell in den Produktionsmodus übergehen. Ein großer Vorteil war, dass die bestehende Linie weiterlaufen konnte. Das reduziert den Druck beim Hochfahren der neuen Anlage.
GW – Sie sprachen auch vom modularen Aufbau der WP-Anlagen – wie ist das zu verstehen?
Hemmerich – Unsere Maschinen sind in Klassen gegliedert – von der XS als Einsteigermodell über die EVO-Mittelklasse bis hin zur SuperHeroes-Baureihe, wie sie jetzt bei Niveau steht. Alle Systeme arbeiten mit der gleichen Zangentechnologie und Bancalata-Logik. Das heißt, Werkstücke gleicher Charakteristik werden gruppiert und gemeinsam präzise bearbeitet. Wir bieten Konzepte von der Einzelteilfertigung über Türenproduktion bis zu industriellen Fensterlinien, alles skalierbar. Und: Wir können bei Bedarf ausgewählte Zusatzbearbeitungen innerhalb der Maschine verlagern oder auf vorgelagerte Bohr-Fräszentren outsourcen, sodass die Balance über die Stationen der Anlage optimiert wird.
GW – Und wie fällt Ihr Fazit zum Projekt aus?
Hemmerich – Niveau hat mutig investiert – und aus unserer Sicht alles richtig gemacht. Der Schritt weg von klassischen Anlagen hin zu einem durchdachten CNC-Hochleistungskonzept bringt langfristig enorme Effizienz. Und die Zusammenarbeit war auf Augenhöhe: offen, ehrlich, partnerschaftlich. So macht Anlagenbau richtig Freude!
GW – Danke für die Auskünfte, viel Erfolg weiterhin!
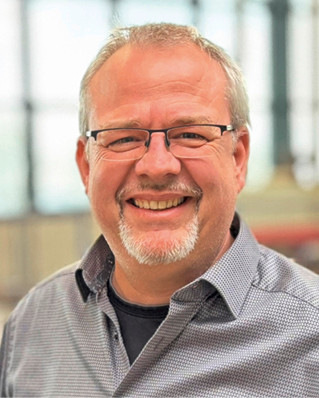
Foto: Daniel Mund / GW
ist seit über 25 Jahren für die Massivholzbranche tätig und spezialisiert in der Fensterproduktion und jetzt das Bindeglied von WP in Deutschland.
Diesen Anlagen-, Werkzeug- und Zuliefer-Unternehmen vertraut Niveau Fenster
www.neumann-spezialmaschinen.de
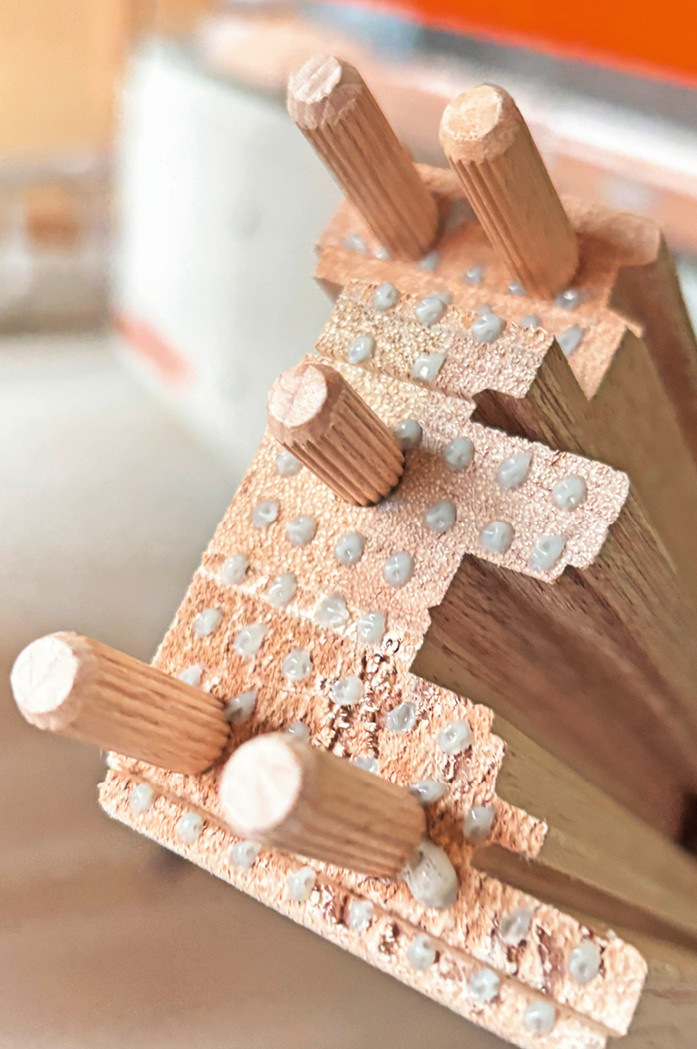
Foto: Daniel Mund / GW